Zkoušky součástí pneumatik
Při pokojové teplotě a obvyklých okolních teplotách v rozmezí -70 až +250 °C se kromě jiných provádí následující zkoušky:
- Zkouška tahem a dalším trháním různých tvarů vzorků z elastomerů
- Zkoušky tvrdosti, odrazu a oděru elastomerů
- Zkouška vytažení ocelových a textilních kordů z elastomerových ložisek
- Zkouška tahem ocelových a textilních kordů, automatizované podávání vzorků z důvodu jejich velkého množství při vývoji nových sloučenin
- Stanovení viskoelastických vlastností
Zkoušky kol
Kola v automobilovém průmyslu se skládají z oceli, lehkých kovů nebo kompozitních materiálů a samozřejmě pneumatik. Pneumatiky představují složité kompozitní součásti vyrobené z materiálů rozličných fyzikálních vlastností. Jako spojovací článek mezi vozovkou a vozidlem přenáší pneumatiky všechny síly a momenty. Ke stanovení kvazistatických a dynamických vlastností kol a pneumatik je možné použít testovací systémy ZwickRoell. Na těchto zkušebních strojích lze provádět celou řadu testů, jako například standardizované zkoušky pryže, textilií a drátů, ale i zkoušky celého systému kola/pneumatik.
Zkoušky pneumatik a kol
Tuhost pneumatik automobilů se určuje měřením poměrů sil při vertikálním a horizontálním zatížení a proměnlivém tlaku vzduchu v pneumatikách. Pro tento účel byla vytvořena kombinace zkušebního stroje AllroundLine 50 kN s horizontální lineární jednotkou a vícesložkovou platformou pro měření síly na spodním příčníku. Pomocí příslušného zkušebního programu v softwaru testXpert lze provádět požadované zkoušky při vertikálním a horizontálním zatížení s různým tlakem v pneumatikách a tyto zkoušky poté vyhodnocovat.
Zkouška osových deformací příruby ráfku
S využitím speciálního tlačného trnu se pro stanovení tuhosti provádějí tlakové zkoušky na lemu ráfku. Zkušební stroj je pro tento účel vybaven dopředu vyčnívajícím, výškově nastavitelným příčníkem s T-drážkami. Tento způsob umožňuje vložení a upevnění ráfků ve zkušebním prostoru v ergonomické výšce. Snímač síly zajišťuje přesné měření složek osových sil, a to i v případě, že se v důsledku tvaru ráfku vyskytují boční síly. Díky své speciální konstrukci a uspořádání může být snímač síly použit pro měření jak v horním, tak i dolním zkušebním prostoru stroje.
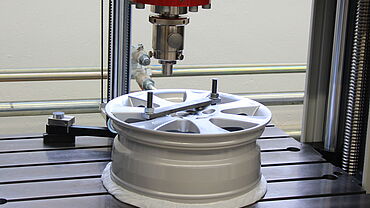
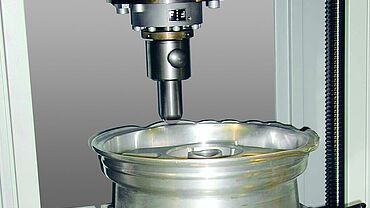
Stanovení celoplošných deformací na lehkém ráfku
Elektromechanický zkušební válec variabilně aplikuje axiální nebo radiální zatížení. Deformační chování zaznamenává optický systém měření deformace 3D. Výsledky zkoušek poskytují informace o možných slabých místech součásti.
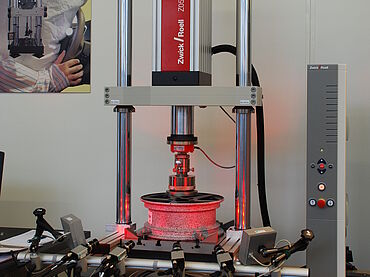
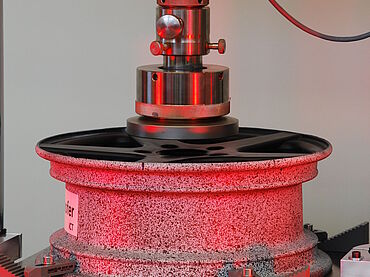
Zkoušky tvrdosti ráfků
Pro kontrolu výroby, ale také pro zajištění pevnostních parametrů se u ocelových a hliníkových ráfků primárně zkouší tvrdost metodou Brinell HBW 2.5 nebo Rockwell, např. HRB. Kromě toho lze aplikovat zatížení až 250 kg pomocí zpětnovazebné smyčky pro všechny tradiční metody zkoušení tvrdosti (tvrdost podle Brinella, Rockwella, Vickerse, Knoopa a kuličková tvrdost) pro kovy a plasty. Na zkušební plochu o rozměrech 250 x 300 mm (D x V) lze snadno umístit i velké součásti.
Zkoušky destiček kotoučových brzd
Destičky kotoučových brzd jsou jednou z nejdůležitějších součástí brzdy kola. Pro hodnocení kvality brzdových destiček se mimo jiné zjišťuje změna tloušťky destiček pomocí jednosměrného tlakového zatížení ve směru kolmém na třecí plochu brzdového kotouče.
Zkušební stroje ZwickRoell jsou pro tento účel jsou vybaveny tlačným zařízením s integrovaným měřicím systémem. Deformace se měří pomocí tří snímačů, které jsou umístěny v úhlu po 120° na kruhové rozteči. Tlak je aplikován pomocí speciálního přípravku pro zkoušky tlakem s kruhovým působením síly. Díky flexibilnímu zavěšení tlačného dílu je umístění přesně rovnoběžné s brzdovým kotoučem, a zajišťuje tak rovnoměrné a homogenní působení tlačné síly. Zkušební poloha tlačného trnu prochází středovou osou plochy destičky kotoučové brzdy. Tím je zajištěno naprosto rovnoměrné a homogenní vyvíjení tlaku.