Batterieprüfung
Die Elektrifizierung des Verkehrssektors wird maßgeblich von Lithium-Ionen-Batterien beeinflusst. Eine Schlüsselrolle bei der Weiterentwicklung von Batteriezellkomponenten, Batteriezellen und Batteriemodulen sowie gesamter Hochvoltspeicher für die Produktion spielen Forschung und Entwicklung, gepaart mit einer umfassenden Qualitätssicherung. Batterieprüfung zur Charakterisierung der verwendeten Materialien und die Generierung von Zwischenproduktmerkmalen sind dabei entscheidende Voraussetzungen für den Fortschritt.
Mit unserer langjährigen Erfahrung in der mechanischen Prüfung im Bereich Elektromobilität bieten wir stets das passende Prüfverfahren entlang der gesamten Wertschöpfungskette für alle verfügbaren Batterievarianten an. Vom Rohmaterial über Werkstoffe, Zellen und Zellkomponenten bis zur finalen Montage im Fahrzeug und dem Recycling – ZwickRoell ist Ihr kompetenter Partner für umfassende Batterieprüfung. Interessante Kundenprojekte
In enger Zusammenarbeit mit führenden Unternehmen der Branche, wissenschaftlichen Einrichtungen und Forschungsinstituten bieten wir ein breites Spektrum an batteriespezifischen mechanischen Prüfverfahren…
Zugversuche Ermüdungsversuche Biegeversuche Druckversuche Schäl-/Adhäsions-/Reibungsversuche Festkörperbatterien Beratung & Vorversuche im Batterieprüflabor Downloads
…sowie funktionalen und strukturellen Prüfverfahren an.
Wie werden Batterien hergestellt? Wo ist die mechanische Batterie-Prüfung wichtig?
- Die Wertschöpfungskette von Lithium-Ionen-Batterien beginnt mit dem Abbau von Rohstoffen wie Lithium, Kobalt, Nickel und Aluminium.
- Nach der Rohmaterialverarbeitung werden die Zellkomponenten, einschließlich Anode, Kathode und Elektrolyt in einem aufwändigen Prozess hergestellt. In diesem Prozess, sprich der Zellkomponentenherstellung, sind Prüfungen wichtig, um einerseits die Qualität und Zuverlässigkeit sicherzustellen sowie andererseits durch die Charakterisierung der Zwischenproduktmerkmale wertvolle Daten für multiphysikalische Simulationen zu generieren.
- Anschließend werden die Batteriezellen produziert und zu Hochvoltspeichern montiert. Auch hierbei spielt die mechanische Batterieprüfung eine entscheidende Rolle, denn sie gewährleistet Funktionalität und Sicherheit der Batterie. Dabei werden Daten ermittelt, um das Verhalten der Batteriezellen und Module im täglichen Einsatz einschätzen zu können.
Mechanische Batterieprüfung: Folien, Elektroden, Separatoren und Zellgehäuse
Die mechanische Batterieprüfung von Folien, Elektroden, Separatoren und Zellgehäuse spielt eine entscheidende Rolle, um nicht nur die Qualität und Leistungsfähigkeit zu gewährleisten und weiter zu entwickeln, sondern auch um eine störungsfreie Produktion sicherzustellen. Zug-, Druck-, Biegeversuche, Ermüdungsversuche und Adhäsionsversuche ermöglichen eine realitätsnahe Charakterisierung dieser Batterie-Komponenten. Außerdem dienen die erhaltenen Daten als Basis für Multiphysics-Simulationen. Diese werden zur numerischen Vorhersage des Verhaltens der Batterie, beispielsweise im Crashfall, eingesetzt.
Zugversuche an Batteriefolien und beschichteten Elektroden
Zugversuche an Batteriefolien und beschichteten Elektroden ermitteln die mechanische Festigkeit und Dehnung.
Die Prüfung von Batteriefolien stellt hohe Anforderungen an die Prüftechnik, insbesondere bei geringen Foliendicken von <10 µm, abhängig vom Einsatzgebiet. Die Gewährleistung belastbarer, wiederholbarer, vergleichbarer und damit sicherer Prüfergebnisse erfordert präzises Probenhandling und eine zuverlässige Probenklemmung. Eine entscheidende Rolle bei der genauen Bestimmung der Werkstoffeigenschaften im Zugversuch spielen daher:
- die vertikale Ausrichtung der Probe
- schonende Klemmtechniken und
- die berührungslose Ermittlung der Längenänderung durch optische Extensometer, wie dem Videoextensometer VideoXtens
Video: Zugversuch Batteriefolie DIN 50154 / ASTM E345
Normen wie die DIN 50154 und die ASTM E345 für den Zugversuch an dünnen Batteriefolien (Aluminium- und Kupferfolien, Polymer-Separatoren) können in den Prüfabläufen berücksichtigt werden, unterstützt durch die ZwickRoell Prüfsoftware testXpert, die eine normgerechte Durchführung gewährleistet.
Durch die aktive Mitarbeit bei der Weiterentwicklung von Normen, speziell für Batteriematerialien, wird sichergestellt, dass die ZwickRoell Prüfverfahren auch zukünftig allen Anforderungen entsprechen.
Zugversuch an Lithium-Metall Folien
Besondere Herausforderungen ergeben sich bei der Prüfung von Lithium-Metall Folien, da deren Zugfestigkeit nur in einer inerten Umgebung bestimmt werden kann. ZwickRoell bietet dafür spezielle Schutzgaskammern (Glove boxes), Probenvorbereitung und Probenmanipulation an. Diese ermöglichen eine präzise Prüfung unter kontrollierten Bedingungen für exakte Ergebnisse.
Zugversuch an Separatorfolien
Separatorfolien in einer Lithium-Ionen-Batterie trennen Anode und Kathode voneinander, um elektrische Kurzschlüsse zu verhindern. Gleichzeitig erlaubt der Separator den Durchfluss ionisierter Ladungsträger, die zum Schließen des Stromkreises in einer elektrochemischen Zelle benötigt werden. Die Effizienz, Lebensdauer und Sicherheit von Batteriezellen hängen maßgeblich von der Funktion dieser Separatoren ab. Prüftechnisch werden die wesentlichen Anforderungen an Separatoren durch Zugversuche nach ISO 527-3 und ASTM D882 sowie Durchstoßversuche nach EN 14477, ASTM D5748 und ASTM F1306 abgedeckt. Diese Tests werden auch im elektrolytbenetzten Zustand durchgeführt, um realitätsnahe mechanische Kennwerte zu erzielen.
Ein weiterer relevanter Aspekt ist das Verhalten des Separators in Bezug auf den Reibungskoeffizienten zwischen Elektrodenbeschichtung und Separator. Diese Kennwerte sind besonders wichtig für die Einstellung der Produktionsparameter in den Wickelprozessen. ZwickRoell ermöglicht nicht nur Prüfungen bei Raumtemperatur, sondern auch bei betriebsnahen Temperaturen im Bereich von -20 °C bis +50 °C mithilfe der ZwickRoell Temperierkammern. Dies gewährleistet eine umfassende Charakterisierung der Separatorfolien unter verschiedenen Bedingungen.
Video: Zugversuch an Separatorfolien
Neben keramischen Separatoren und Glasfaservliesstoffen werden primär Polymer-Membranen eingesetzt. Die verlässliche Ermittlung der Zugfestigkeit und Bruchdehnung gibt Rückschlüsse über die Integrität der Separatorfolie unter betriebsbedingter mechanischer Belastung.
Während stärkere Separatorfolien den Kontakt zwischen Anode und Kathode effizient und sicher verhindern, ermöglichen dünnere Folien das Gewicht der Batterie zu reduzieren und die Energiedichte zu verbessern. Zugversuche an Separatorfolien werden nach den genormten Verfahren ASTM D882 und ISO 527-3 durchgeführt.
Um Zugversuche an Batteriefolien und beschichteten Elektroden automatisiert durchführen zu können steht unser Roboter-Prüfsystem roboTest F zur Verfügung, welches speziell für die automatisierte Prüfung nicht formstabiler Proben entwickelt wurde.
Haben Sie Interesse mehr über unsere Automatisierungsmöglichkeiten in der Batteriefolien-Prüfung zu erfahren?
Wir beraten Sie gerne!
Ermüdungsversuche an Batteriefolien
Batteriefolien aus Kupfer und Aluminium fungieren als Stromsammler in Lithium-Ionen-Batterien und sind verschiedenen Belastungen sowohl während des Produktionsprozesses als auch im Batteriebetrieb ausgesetzt.
- Während des Produktionsprozesses können Beschichtungsfehler wie Fehlstellen oder Ungleichverteilungen auftreten. Obwohl der Kalandrierungsprozess solche Fehler mildern kann, lassen sie sich nicht vollständig beseitigen.
- Im Batteriebetrieb unterliegen die Folien thermischen und mechanischen Belastungen, die zu Ermüdungserscheinungen führen können. Zudem können chemische Reaktionen mit Elektrolyten Korrosion verursachen, was die Batterieleistung beeinträchtigt.
Es ist entscheidend zu beachten, dass spezifische Belastungen und Ermüdungserscheinungen von vielen Faktoren abhängen, darunter das Batteriedesign und die Betriebsbedingungen. Daher erfordert die Batterieentwicklung und -optimierung stets eine gründliche Untersuchung und Charakterisierung von Batteriefolien durch Ermüdungsversuche.
Durch die kleinen Prüfkräfte der elektrodynamische Prüfmaschine LTM können Ermüdungsversuche gerade bei empfindlichen Proben problemlos durchgeführt werden. Die LTM ist mit einer ölfreien Antriebstechnologie ausgestattet. Der Linearmotor ist besonders leise und bestens für den Einsatz im Labor geeignet.
Um die Batteriefolie nicht durch die Messschneiden zu beschädigen wird die Dehnungsveränderung mit einem optischen Video-Extensometer videoXtens dynamic gemessen.
Biegeversuche an Elektrodenbeschichtungen
Biegeversuche zur Ermittlung der Biegefestigkeit der Aktivmaterial-Beschichtung ist für die Lebensdauer von Lithium-Ionen Batterien von großer Wichtigkeit.
Das Aktivmaterial der Elektroden besteht aus einer 50–100 µm dicken Beschichtung, deren mechanische Eigenschaften aufgrund der chemischen Zusammensetzung und des Produktionsprozesses stark variieren können. Diese Kenntnisse sind essenziell, um optimale Einstellungen der Produktionsparameter, wie Durchlaufgeschwindigkeit, Rollenwinkel und Vorspannkräfte, zu definieren. Die Ermittlung der Biegefestigkeit mittels einer 2-Punkt-Biegevorrichtung ermöglicht die Bestimmung des maximal zulässigen Biegewinkels und Biegeradius, bei dem die Beschichtung intakt bleibt und der Kontakt zwischen Ableiterfolie und Aktivmaterial erhalten bleibt. Hierbei erweist sich die Prüfmaschine zwickiLine mit 2-Punkt-Biegevorrichtung und integriertem hochauflösendem Kraftaufnehmer als geeignete Prüfmaschine.
Druckversuche für Batteriefolien, Aktivmaterial und beschichtete Elektroden
Der Druck, mit dem die Elektroden- und Separatoren-Schichten gestapelt werden, ist entscheidend für eine effektive Kontaktierung innerhalb der Zelle. Dieser Druck beeinflusst maßgeblich die Lebensdauer und Leistungsfähigkeit der Zelle.
ZwickRoell bietet verschiedene Arten des Druckversuchs für Batteriefolien, Aktivmaterial und beschichtete Elektroden an, um diese dynamischen Belastungszustände präzise zu simulieren und zu charakterisieren.
- Der Kalandrierprozess spielt eine zentrale Rolle in der Herstellung von Elektroden für Lithium-Ionen-Batterien. Dabei wird eine Paste aus Aktivmaterial, Bindemittel und Leitadditiv auf eine Metallfolie (Kupfer für die Anode, Aluminium für die Kathode) aufgetragen. Durch Walzen, die unter Druck und Temperatur arbeiten, wird die beschichtete Folie zu einer dünnen, gleichmäßigen Schicht gepresst.
- Die Energiedichte von Lithium-Ionen-Batteriezellen, die die Reichweite elektrisch angetriebener Fahrzeuge maßgeblich beeinflusst, hängt wesentlich von diesem Prozessschritt ab. Die Variation der Prozessgrößen ermöglicht die Optimierung von Anlagen- und Materialparametern.
- Druckverformungsmessungen sind von großer Relevanz, da sie dazu beitragen, die Qualität und Konsistenz der Elektroden zu überwachen und zu kontrollieren. Diese Messungen geben Aufschluss darüber, wie gut das Aktivmaterial in die Elektrode eingebettet ist und ob es während des Batteriebetriebs zu Ablösungen kommen könnte. Zudem tragen sie dazu bei, den optimalen Druck und die optimale Temperatur für den Kalandrierprozess zu ermitteln, um eine maximale Energiedichte und Leistung der Batterie zu erreichen.
Multifunktionale Analyse beschichteter Elektroden und prototypischer Zellstacks (jelly rolls)
Bei der Prüfung von beschichteten Elektroden und prototypischer Zellstacks ist die Charakterisierung der Materialien und Komponenten wichtig, um deren Effizienz, Leistung und Lebensdauer langfristig zu gewährleisten. Diese Kennwerte sind für Forschung und Entwicklung als auch für die Qualitätssicherung von entscheidender Bedeutung.
ZwickRoell hat hierzu den Multifunctional Cell Component Analyzer (MCCA) entwickelt. Mithilfe von drei hochgenauen linearen Wegmessern und einer Nivelliereinheit kann Druck exakt auf eine Fläche der Elektrode appliziert werden. Dies ermöglicht die genaue Messung der Dickenänderung der Elektrode unter realistischen Druckbedingungen. Gleichzeitig wird der elektrische Widerstand über vergoldete Druckplatten gemessen, was eine Auswertung in Abhängigkeit vom Druck erlaubt.
Während des elektrischen Lade- und Entladevorgangs kommt es zu einem An- und Abschwellen der Zelle, bekannt als "Battery Swelling". Dies führt zu Veränderungen im Druck auf die einzelnen Komponenten. Die MCCA-Prüfvorrichtung ermöglicht hochpräzise „Battery Swelling“-Versuche an prototypischen Elementarzellen wie beispielsweise Coin Cells und trägt dazu bei, das Verhalten im Lade- und Entladezyklus des kleinsten sich wiederholenden Zellkomponentenstapels in der Jelly roll präzise zu charakterisieren.
Vorteile des Multifunctional Cell Component Analyzer:
- Hochpräzise Messung des Spannungsdehnungsverhaltens beschichteter Elektroden unter Druck
- Messung des elektrischen Widerstands in Abhängigkeit des Drucks
- Messung des „Battery Swelling“-Verhaltens prototypischer Elementarzellen (Coin Cells)
Hochpräzise Druckversuche im Elektroden-Beschichtungsprozess
Eine große Herausforderung in der Batterieproduktion ist der Beschichtungsprozess der Elektroden. Für einen sicheren Batteriebetrieb werden wichtige Kriterien sichergestellt: eine ausgezeichnete mechanische Stabilität, exzellente elektrische Leitfähigkeit und ein vorhersehbares Alterungsverhalten des Aktivmaterials. Die Beschichtungstechnologien für Elektroden werden kontinuierlich weiter verbessert und die vielversprechende Entwicklung der Trockenbeschichtung muss neben dem sehr hohen Energieeinsparungspotenzial ähnliche oder bessere funktionale Elektrodeneigenschaften sicherstellen.
- Dazu ist eine detaillierte Analyse des Verhaltens von Batteriefolien, wie Separatoren und beschichteten Elektroden unter Druck wichtig. Durch den instrumentierten Kompressibilitätsmesskopf werden genaue Kraft-Weg-Kurven erstellt, wodurch das elastische Verformungsverhalten im Druckversuch für extrem dünne Schichten ermittelt werden kann. Dies liefert essenzielle Daten für die Materialentwicklung, Qualitätssicherung und Batteriesimulation.
- Die sichere Verbindung zwischen Aktivmaterial und dem Elektrodensubstrat ist entscheidend für Qualität und Leistungsfähigkeit einer Batteriezelle. Um eine optimale mechanische Stabilität des Aktivmaterials zu gewährleisten, müssen dessen Porosität und Leitfähigkeit unter wechselndem Betriebsdruck erhalten bleiben.
Bestimmung des Setzverhaltens von Separatorfolien
Bei den für Separatorfolien verwendeten Materialien kann unter zyklischer Druckbelastung ein Setzverhalten auftreten. Dieses Setzverhalten, das zu einer Veränderung der Folienstärke führt, beeinträchtigt mitunter die Leistungsfähigkeit und Lebensdauer der Batterie. ZwickRoell bietet mit den universellen Zug-Druckprüfmaschinen sowie den speziellen Prüfständen für Druckversuche, MCCA und Nanoindenter, eine vielfältige Palette von Versuchsmethoden zur Charakterisierung des Setzverhaltens von Separatorfolien.
Schäl- und Adhäsionsversuche in der Batterieprüfung
Neben den mechanischen Kennwerten ist auch die Haftfestigkeit der ein- oder doppelseitigen Beschichtungen auf der Ableiterfolie von entscheidender Bedeutung, da diese Verbindung maßgeblich für die interne Leitfähigkeit der Batterie verantwortlich ist. Da sich die Haftfestigkeit mit dem Alter der Batterie ändern kann, ist es wichtig sicherzustellen, dass die Verbindung dauerhaft gewährleistet ist. Dies kann durch Schäl- und Adhäsionsversuche sichergestellt werden. Ablösungen des Aktivmaterials, die im Elektrolyt treiben, beeinträchtigen erheblich die Zellensicherheit. Daher ist die Überprüfung der Adhäsionskraft der Elektrodenbeschichtung sowohl an Anode als auch Kathode von großer Bedeutung für die Produktionsüberwachung direkt an der Zellfertigungslinie.
Die mechanische Haftfestigkeit zwischen Aktivmaterial und Substrat wird auf unterschiedliche Arten ermittelt:
90° und 180° Schälversuche
Die gängigste Methode die mechanische Haftfestigkeit zwischen Aktivmaterial und Substrat zu ermitteln, ist der Schälzugversuch mit einem Schälwinkel von 90° oder 180°.
- Bei beiden Varianten wird die beschichtete Folie auf einem Trägermaterial aufgebracht und dann im vorgegebenen Schälwinkel von der Prüfmaschine abgezogen.
- Die Verfahren sind nicht genormt und daher nur sehr schwierig vergleichbar zu gestalten.
- Die wichtige qualitative Beurteilung der Versagensart (Kohäsions- oder Adhäsionsbruch) ist mit diesem Verfahren nur bedingt möglich.
- Weitere Nachteile dieser Prüfungen sind der hohe Materialverbrauch und die aufwendige Probenvorbereitung.
Video: Schäl-, Durchstoß- und Biegeversuche an Batteriefolien
- 90° / 180° Schälversuche zur Ermittlung der mechanischen Haftfestigkeit zwischen Aktivmaterial und Substrat für QS sowie F&E.
- Durchstoßversuche an Separatorfolien zur Ermittlung der Durchstoßfestigkeit, um Sicherheitsprobleme zu vermeiden, da die Folie definierten Widerständen gegen mechanische Einflüsse widerstehen muss.
- 2-Punkt-Biegeversuche zur Charakterisierung der Biegefestigkeit verschiedener Materialien, um Abweichungen von vorgegebenen Parametern festzustellen, die zu Produktionsbrüchen und Sicherheitsproblemen führen können.
Z-Direction Adhäsionstest
Eine verlässlichere und reproduzierbarere Ermittlung der Haftfestigkeit sowie der Bewertung der Versagensart, ist der Z-Direction Adhäsionstest. In die Haftzugsvorrichtung „Z-Direction" können fünf Proben gleichzeitig mittels einer Probenvorrichtung vorbereitet werden . Zudem führt die Prüfmaschine automatisiert die definierten Parameter Anpressdruck und –dauer identisch für jede einzelne Probe durch. Diese Prüfvorrichtung trägt dazu bei Bedienereinfluss auf das Messergebnis im Vergleich zu Schälversuchen zu reduzieren.
Anschließend wird jede einzelne Probe in Z-Richtung abgezogen und ein deutlicher maximaler Haftfestigkeitswert ermittelt. Neben einer sehr effizienten Probenvorbereitung und einer hohen Wiederholgenauigkeit ermöglicht dieses Verfahren auch eine eindeutige Bestimmung der Kohäsions- und Adhäsionsanteile des Bruchbildes. Die gute Vergleichbarkeit der Ergebnisse, die mit diesem Versuchsverfahren erzielt wurde, ermöglicht gleichzeitig eine zuverlässige Überwachung der Beschichtungsqualität im Produktionsprozess.
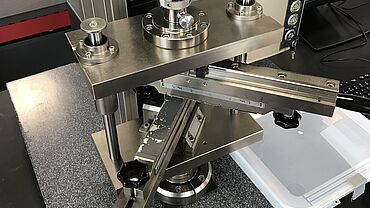
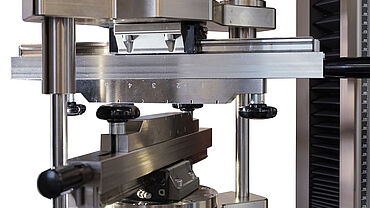
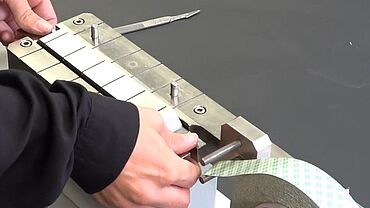
Video: Adhäsionstest an Elektrodenbeschichtungen
Die Haftfestigkeitsprüfung in Z-Direction ist ein zuverlässigeres und reproduzierbares Verfahren zur Bestimmung der Haftfestigkeit zwischen Aktivmaterial-Beschichtungen und Elektroden (Al- oder Cu-Folie) an Lithium-Ionen Batterien und zur Beurteilung der Art des Versagens.
- In der Qualitätssicherung sind Schälversuche ein wichtiger Indikator für die Prozesssicherheit, wenn es um die Haftfestigkeit der Beschichtung geht. Je besser die Haftfestigkeit, desto besser die Leistung und Lebensdauer der Batterie.
- Wenn Sie in der Forschung und Entwicklung tätig sind, helfen unsere Schälversuche, die Kombinationsmöglichkeiten verschiedener Materialien zu optimieren und damit die Batterieleistung zu erhöhen.
Reibungsversuche an Elektrodenbeschichtungen, Ableiterfolien und Separatoren
Die Bestimmung des Reibungskoeffizienten von Elektrodenbeschichtungen, Ableiterfolien und Separatoren in der Produktion von Lithium-Ionen-Batterien ist von entscheidender Bedeutung, um potenzielle Probleme während des Fertigungsprozesses zu identifizieren und die Qualität sowie die Leistung der Batterien sicherzustellen.
Mögliche Reibungsversuche sind:
- Schichtadhäsionstest: Die Haftung zwischen den verschiedenen Schichten wird in der Batteriezelle untersucht. Das Anwenden einer definierten Kraft oder Belastung ermöglicht die Bewertung der Tendenz der Schichten, sich zu trennen oder zu haften. Die resultierenden Schichttrennkräfte ermöglichen Rückschlüsse auf die Reibkoeffizienten.
- Kontaktkraft- und Verschiebungstest: Diese Prüfungen messen die Kraft, die erforderlich ist, um Materialien mit unterschiedlichen Beschichtungen oder Oberflächen miteinander zu verschieben oder zu trennen. Dadurch kann das Verhalten der Materialien unter Druck verstanden und der Reibkoeffizient quantifiziert werden.
Da es generell und auch für diesen Anwendungsfall noch wenige spezielle Prüfnormen für EV-Batterien gibt, können die ASTM D1894 und die ISO 8295 als Ersatznormen für die Charakterisierung ihrer Reibungseigenschaften verwendet werden. Diese Tests werden auch im elektrolytbenetzten Zustand durchgeführt, um realitätsnahe mechanische Kennwerte zu erzielen.
Charakterisierung von Festkörperbatteriekomponenten
Mit dem Wegfall des Flüssigelektrolyten bei Festkörperbatterien entstehen neue Herausforderungen wie Grenzschichtkontaktierung, thermische Ausdehnung und Alterungsbeständigkeit. Für die Charakterisierung von Festkörperbatteriekomponenten bietet ZwickRoell umfangreiche Prüfverfahren für die speziellen Anforderungen bei Festkörperbatterien.
- Die mechanische Charakterisierung einer Anode aus Lithium-Metall kann herausfordernd sein. Die Probenvorbereitung und die Bestimmung der Zugfestigkeit müssen aufgrund der starken Degradation in einer Inert-Gasen Umgebung erfolgen. Zudem erfordert der empfindliche, duktile Werkstoff eine äußerst vorsichtige Handhabung in speziellen Probenklemmen und die sichere Ermittlung der Längsdehnung mit einem optischen Extemsometer. ZwickRoell bietet dafür spezielle Schutzgaskammern (Glove boxes), Probenvorbereitung und Probenmanipulation, sowie einen angepassten optischen Extensometer mit dem die Messung ohne Berührung der Probe möglich ist.
- Eine weitere Herausforderung besteht in der Ermittlung der mechanischen Eigenschaften weiterer Komponenten wie der Composite-Kathode oder des Festkörperelektrolyt-Separators. Die Festigkeiten dieser Komponenten beeinflussen maßgeblich die Auslegung der Fertigungsprozesse und die sichere Funktionalität im Batteriebetrieb. Mit einem ZHN-Nanoindenter können Festelektrolyten aus Polymeren, Oxiden oder Sulfiden mit unterschiedlichen mechanischen Eigenschaften charakterisiert werden, um Elastizitätsmodul, Härte, Biegefestigkeit und Bruchzähigkeit zu untersuchen.
Funktionale und strukturelle Batterieprüfung: Batteriekomponenten, Zellen und Zellverbunde
Die funktionale und strukturelle Prüfung von Zellen und Zellverbindungen spielt eine entscheidende Rolle bei der Montage von Zellen zu Modulen und Packs sowie für die Sicherheit im Batteriebetrieb. Battery Swelling, das Anschwellen der Batterien während des Lade- und Entladevorgangs, wird durch hochpräzise Swelling-Tests ermittelt, um es in den weiteren Schritten zu berücksichtigen. Der vorherrschende Druck in der Zelle wird in Quetsch- und Biegetests untersucht, einschließlich Missbrauchsversuchen wie dem Nageldurchstoßversuch.
Battery Swelling Test: Charakterisierung des Zellverhaltens im Lade- und Entladezyklus
Das Verhalten der Batteriezellen während des Lade- und Entladevorgangs, insbesondere die Ausdehnung der Zellen, das sogenannte "Battery Swelling" oder "Battery Breathing", beeinflusst die Leistungsfähigkeit und Langlebigkeit. Dieses Phänomen zeigt sich besonders deutlich bei prismatischen Zellen und Pouchzellen, sowie bei Festkörperbatterien. Aber auch das Verständnis der Ausdehnung von zylindrischen Zellen gewinnt zunehmend an Bedeutung in der Entwicklung neuer Batteriegenerationen.
Die präzise Charakterisierung dieses Verhaltens unter gleichzeitiger Temperierung ist entscheidend. Dabei muss die Atmung der Zelle für den Zusammenbau im Modul berücksichtigt werden, da die Ausdehnung der Zellen im Modul zu einer Änderung des Drucks auf die Zelle führt. Dieser Druck und die Temperatur beeinflussen erheblich die Langlebigkeit und Leistungsfähigkeit der Zellen. Daher ist die genaue Charakterisierung der Zellatmung und des Swellings bedeutend. ZwickRoell bietet verschiedene Herangehensweisen zur Charakterisierung des Zellverhaltens im Lade- und Entladezyklus einschließlich elektrischer Zyklisierung, hochgenauer Verformungsmessung, langfristiger Testabläufe und der kontrollierten Temperierung.
- Temperierung der gesamten Batteriezelle
Die Batteriezelle wird mithilfe einer Temperierkammer auf eine gewünschte Betriebstemperatur erwärmt, die für die Prüfdauer in der Kammer konstant gehalten wird. Geregelt wird hier nach der Umgebungstemperatur in der Temperierkammer. Die Sicherheit während des Versuchs wird, je nach Risiko, über die Temperier- bzw. eine Schutzkammer mit passendem Hazard Level gewährleistet. - Präzise und homogene Temperierung der gesamten Batteriezelle
Durch das aktive Heizen und Kühlen der Druckplatten wird einerseits die Oberflächentemperatur der Batteriezelle von oben und von unten homogen temperiert und präzise geregelt. Andererseits können auch lokale Temperaturschwankungen innerhalb der Batteriezelle ausgeglichen werden. Kritischen Temperaturen bei beispielsweise hohen Entladeströmen wird somit entgegengewirkt und eine zuverlässige Prüfung sichergestellt.
Diese Art der Prüfung wurde in einer Kooperation mit der Firma MBTS entwickelt. In einem Artikel wurde nun der Einfluss von unterschiedlichen Temperaturen, Drücken und Entladeraten auf die elektrischen Eigenschaften einer standardisierten Lithium-Ionen Batteriezelle für automotive Anwendung unter die Lupe genommen.
Zum Artikel
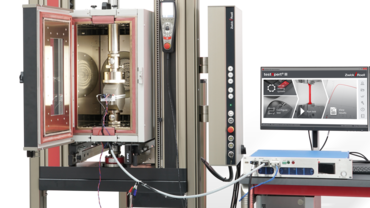
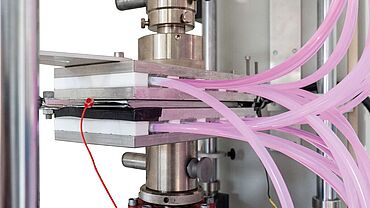
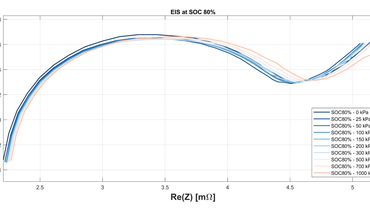
Battery Abuse Testing
Battery Abuse Tests, auch Missbrauchstests genannt, sind zerstörende Sicherheitstests für Lithium-Ionen Batterien. Diese Tests sind für das Inverkehrbringen und den Einsatz von Batterien in automobilen Anwendungen erforderlich. Bei den Tests wird die Batterie extremen Bedingungen ausgesetzt, um ihre Sicherheit und Zuverlässigkeit zu gewährleisten. Zu den typischen Missbrauchstests gehören neben thermischen und elektrischen Prüfungen auch mechanische Prüfungen.
Bei mechanischen Prüfungen wird die Batterie physisch beansprucht, indem ein Gegenstand in sie eindringt oder sie mechanisch belastet wird, um ihre Integrität zu testen. Dabei wird beispielsweise untersucht, wie eine Nagelpenetration (Nailing), die einen internen Kurzschluss verursacht, oder eine Quetschung (Crash) die Funktionalität und das sicherheitstechnische Verhalten der Batterie beeinflusst.
Diese sogenannten Battery Abuse Tests führen typischerweise zu einem thermischen Durchgehen (engl. Thermal Runaway), das in Brand oder Explosion münden kann. Aufgrund von Umweltauflagen und Arbeitssicherheitsbewusstsein dürfen diese Tests nicht in freier Umgebung oder alten Gebäuden ohne Abgasaufbereitung durchgeführt werden, um reproduzierbare Umgebungsbedingungen sicherzustellen.
Mit der Universalprüfmaschine Allroundline Z100 von ZwickRoell und der weisstechnik Extreme Event Kammer können Battery Abuse Tests mit einer maximal Kraft von 100 kN durchgeführt werden. Dank der mechanischen Modularität können Prüfwerkzeuge einfach und sicher gewechselt und verschiedene mechanische Missbrauchsprüfungen auf einer Maschine sicher durchgeführt werden. Die Auswertung der Prüfergebnisse erfolgt mit der Prüfsoftware testXpert.
Umfassendes Know How in der Materialprüfung, Zugriff auf sämtliche hochpräzise Prüfmaschinen und das gesamte Zubehör-Portfolio in unserem ZwickRoell Batterie-Testzentrum stehen für Ihre Beratung in der Anwendungstechnik zur Verfügung.
Sie haben Interesse an kostenlosen Vorversuchen in unserem Batterie-Testzentrum? Wir beraten Sie gerne bei der Auswahl der richtigen Prüfausrüstung.
Die mechanische Prüfung spielt sowohl bei der Weiterentwicklung der Batterietechnologie als auch bei der Qualitätssicherung in der Batterieproduktion eine Schlüsselrolle. Große materialseitige Herausforderungen aber auch multiphysikalische Anforderungen (Mechanik, Temperatur, Elektrizität) erfordern eine enge Zusammenarbeit zwischen Batteriekunde und Prüfhersteller. Wir haben es uns zur Aufgabe gemacht, für und mit unseren Kunden das bestmögliche Prüfkonzept zu erarbeiten.
Unser neues Batterie-Prüflabor verfügt über modernste Prüftechnik, um unterschiedliche mechanische Batterieprüfungen zur Zellcharakterisierung sowohl im Bereich der Forschung und Entwicklung als auch der Produktion von Batterien durchzuführen. Zwei Anwendungsexperten stehen unseren Kunden sowohl für Versuche vor Ort oder Remote zur Verfügung. Auf diese Weise wollen wir sicherstellen, dass wir das bestmögliche Prüfkonzept für die jeweiligen Anforderungen unserer Kunden finden.
Schauen Sie sich gerne virtuell in unserem Labor um oder kontaktieren Sie uns noch heute – wir beraten Sie gerne!
Interessante Projekte in der Batterieprüfung
Je nach Anwendungsbereich gibt es verschiedene Batterietypen mit vielfältigen Eigenschaften. Die Bekanntesten: Lithium-Ionen-Batterien. Sie kommen in vielen elektronischen Geräten und Elektrofahrzeugen (EV battery, Electric Vehicle Battery) zum Einsatz. Außerdem gibt es eine Vielzahl unterschiedlicher Zellchemien, die sich ständig weiterentwickeln. Zellchemien führen zu heterogenen Batterieeigenschaften, weshalb eine präzise Charakterisierung auch mechanisch wichtig ist. Zellformate, wie zylindrische, prismatische und Beutelzellen, bieten mannigfaltige Vor- und Nachteile in Bezug auf Energiedichte, Platzbedarf und Leistungsfähigkeit. Daher hängt die Auswahl des passenden Batterietyps und Zellformats auch stets ab von den spezifischen Anforderungen der jeweiligen Anwendung. Zusammenfassend kann gesagt werden, dass es sich im Bereich der Batterieentwicklung und /–produktion um eine große Vielfalt an unterschiedlichen Ansätzen handelt. Somit ist auch eine Vielzahl an Prüfverfahren notwendig.