Universal Testing Machines for Static Applications
Our universal testing machines for static applications are specially designed for tensile tests, compression tests, flexure tests and shear tests. They are ideal for standard tests, but also for complex test tasks in the field of materials and components testing.
Universal testing machines (UTMs) thereby provide a flexible solution for tests on a wide variety of materials and components for applications in any industry. Whether it be for low test forces or large loads, quality control or research projects, universal testers provide excellent reproducibility of test results.
Products What is a universal testing machine? Customer projects Operation FAQS
What is a universal testing machine?
A UTM or universal testing machine is referred to as universal because it can be used to perform a variety of static tests, including tensile tests and compression tests, as well as flexure tests, peel tests, tear tests and other mechanical tests. It can run a wide variety of standard-compliant tests on an even larger number or materials for many different applications in essentially every industry. A typical UTM machine consists of a load cell, crosshead, extensometer, specimen grips, electronics, and a drive system. It is controlled by testing software used to define machine and safety settings, and store test parameters defined by North American and international test standards such as ASTM and ISO. The amount of force applied to the machine and the elasticity and compressive fracture properties (compression direction), or elongation properties (tensile direction) of the specimen are recorded throughout the test. Measuring the compressive or tensile strength of materials helps designers and manufacturers predict how materials will perform when implemented for their intended purpose.
ZwickRoell universal testing systems, including the zwickiLine, ProLine, AllroundLine, and E-series machines, are modular systems that can be adapted to meet specific customer requirements based on testing capacity, types of material, applications, and industry standards such as ASTM E8 / ISO 6892-1 and ISO 6892-2 for metals, ASTM D638 / ISO 527 for plastics, ASTM D412 for tensile tests on rubber and elastomers, ASTM D575 for compression tests on rubber, and many more. ZwickRoell also offers several universal testing machines specifically designed for special applications. In addition to overall system safety and reliability, ZwickRoell designs and builds every universal materials testing machine with a focus on providing:
- A high level of flexibility through ease of operation
- Simple adaptations to customer- and standard-specific requirements
- Future-proof expansion capabilities to grow with your needs
How does a universal testing machine work?
A materials testing machine that is categorized as universal can be used to perform tests in tensile and compression direction on a wide range of materials for many different applications. The universal tester tends to be modular in design, which allows the user to switch from compression direction (pressing) to tensile direction (pulling), and test at loads ranging from 0.5 kN up to 5,000 kN and at a high test-speed range that can be used without restriction.
Tensile test
For a typical tensile test, the universal testing machine is set up with the specimen grips that correspond to the type of material to be tested. The right test parameters (force, speed, gauge length, etc.) are configured, the specimen is gripped on each end with the appropriate type of specimen grips and pulled apart until it breaks. The universal tensile testing machine measures the strength (tensile strength), elongation and stiffness (tensile modulus) of the specimen and records it.
Compression test
The universal testing machine can be re-configured and physically converted for a compression test or flexure test.
For a typical compression test, the machine is set up with the appropriate compression fixtures for the type of material to be tested. The corresponding test parameters are then configured, and the specimen is placed between two compression platens until a specified load or distance has been reached, or until the specimen breaks. Common measurements include the elastic limit, the proportionality limit, the yield point, and the compressive strength.
Flexure test
However, the universal testing machine can also be reconfigured and converted for a flexure test.
A flexure test is a compression test in which the specimen is positioned over two supports and loaded in the middle with a die. A compression force is then applied on the unsupported section of the specimen from above until a specified load or distance has been reached, or until the specimen breaks. The flexural strength is the material’s ability to resist deformation under load and is measured in terms of stress. The universal testing machine can be configured to perform a three-point or four-point flexure test.
Frequently asked questions about universal testing machines
A UTM or universal testing machine is referred to as universal because it can be used to perform a variety of static tests, including tensile tests and compression tests, as well as flexure tests, peel tests, tear tests and other mechanical tests. It can run a wide variety of standard-compliant tests on an even larger number or materials for many different applications.
A universal testing machine can be used for many different tests on a wide variety of materials, including tensile and compression tests, flexure tests, peel and adhesion tests, hardness tests, torsion tests, and more.
First, the specimen is gripped in the jaws of the universal testing machine. The specimen is then uniformly stretched until it breaks. During the full duration of the test, the strain and the tensile force are measured, recorded and evaluated.
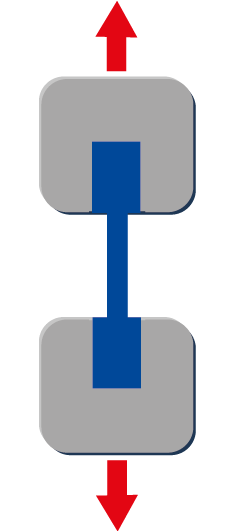
The specimen or component is placed between two compression platens installed in the materials testing machine. The machine crossheads move the platens together with a specified force, speed and/or crosshead travel distance. The required values are measured and recorded.
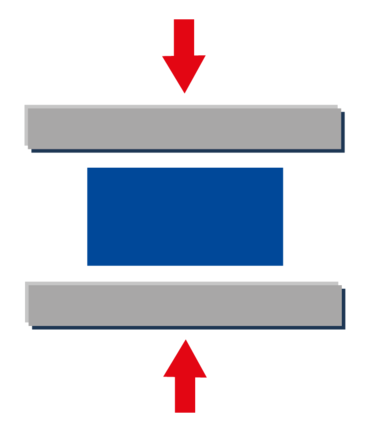