Aerospace Testing
The aerospace industry represents a key technology of great economic and strategic importance. Developments for autonomous and unmanned flying—Advanced Air Mobility (AAM) and Unmanned Air Systems (UAS)—are currently in full swing amidst major advances in flight management and control systems. In today’s New Space Era, private companies are collaborating with established space organizations and eagerly working to develop their own rocket launch systems worldwide in order to meet the growing demand for space launch services. With a goal of leading the aviation industry into a sustainable future, the development of drive systems based on Sustainable Aviation Fuels (SAF) in the medium term and hydrogen in the longterm is being accelerated. Existing fleets are being modernized and the demand for aircraft maintenance, repair and overhaul (MRO) is constantly increasing.
With testing systems for materials testing at cryogenic temperatures of -253 °C (20K) up to high-temperature testing systems of up to 2000 °C, we help our customers develop ever more efficient lightweight materials and structures. Discover our expertise, longstanding experience and in-depth understanding of applications for mechanical testing of metallic materials, fiber-reinforced plastics and sandwich composites, ceramic materials and for the testing of fasteners used in the aerospace industry. Static and dynamic materials testing machines from ZwickRoell are used by our aerospace customers around the world at all technology readiness levels (TRL), and support NADCAP accredited testing solutions.
Metals Composites High-temperature Cryogenic temperatures Fasteners Hardness testing Customer projects
Aluminum alloys are widely used in aerospace structures due to their favorable weight-specific characteristics, and their established manufacturing processes and calculation methods. Titanium alloys, another class of light metals, also have very favorable weight-specific characteristics, much higher corrosion resistance when compared to aluminum, and very good high-temperature characteristics. They are therefore particularly used for mechanically highly-stressed components and for engine components. On a smaller scale, high-strength steel alloys can be found in structural components that are also subject to equally high stresses.
Major advances in additive manufacturing processes for metals now make it possible to design highly complex lightweight structures that could not previously be realized using conventional manufacturing processes. Metallic materials, especially light metals and their alloys, play a key role in the design and manufacturing of aircraft and space systems.
Important test standards for metals
In addition to static test methods, fatigue tests on metallic materials play a prominent role in determining the behavior of metallic materials used in aerospace structures under real load conditions. With our testing systems, ZwickRoell covers all common metals standards. In addition to standardized solutions we offer different levels of customized adaptations and automated testing systems for metals.
Fiber-reinforced plastics and sandwich composites
Due to their outstanding weight-specific mechanical properties, fiber-reinforced plastics and sandwich composites are firmly established for lightweight structures used for aerospace technology. Laminates made of carbon fiber-reinforced plastics (CFRP), in particular, support simplified construction and design of aerospace structures due to their advantageous fatigue properties. The higher corrosion resistance when compared to well-established metallic materials is another reason for the use of fiber-reinforced plastics in this industry. The aerospace industry has been and continues to be a pioneer in the continuous development of composite material systems, manufacturing processes and mechanical test methods for the characterization of composite laminates and sandwich composites.
In addition to a wide range of static and dynamic tests at ambient temperature, tests on composites for aerospace structures are also often performed in a defined temperature range from -55 °C (-67 °F) to 121 °C (250 °F). Currently, the development of alternative and sustainable drive concepts, which has intensified considerably in recent years, and the storage of liquid hydrogen at cryogenic temperatures, which is the most favorable option for larger aircraft, are bringing static and fatigue tests at ultra-low temperatures of -253 °C (20K) increasingly into the limelight.
Important composites test standards in the aerospace industry
Test method | Standard | Airbus / Boeing factory standards |
---|---|---|
Composites tensile tests |
|
|
Composites compression tests |
| |
In-plane shear tests |
|
|
Composites flexure tests |
| |
Interlaminar shear strength ILSS |
| |
Compression after impact CAI |
|
|
Bearing response and joint strength |
|
|
Interlaminar energy release rate |
|
|
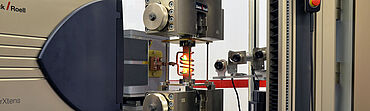
To determine the high-temperature behavior of metallic materials used in aircraft engines, predominantly tensile tests up to 1,200 °C are performed using a static materials testing machine equipped with a high-temperature furnace. The combination of the testing machine with a standard temperature chamber and a high-temperature furnace covers an even wider temperature range from low temperatures up to 1,200 °C. To determine the reliability and durability of highly stressed components under extreme conditions, high-temperature metals are also subjected to creep tests and creep fatigue tests to determine creep limits and creep strength characteristics at different temperature levels. This helps our customers understand the behavior of new high-temperature alloys, to select the right material for a specific application, and provides suitable data for the design of components exposed to high temperatures.
The mechanical load capacity of ceramic matrix composites (CMCs) can also be tested at extremely high temperatures of up to 2,000 °C. The suitability of CMCs for specific applications is evaluated on the basis of tensile, compression, shear, bending, creep and creep fatigue tests. To ensure that the CMCs are tested under real operating conditions, the tests can be carried out under vacuum and inert gas conditions in a temperature range from 650 °C to 2,000 °C.
High-temperature testing systems from ZwickRoell also support non-contact strain measurement up to the maximum temperature. Premature failure of sensitive specimens caused by indentations from conventional contact measuring systems can therefore be ruled out. An automatic and adaptive high-temperature controller ensures high-precision temperature control and prevents operator errors. The use of sacrificial test specimens often required for high-temperature tests is no longer necessary.
More on high-temperature testing More on high-temperature testing systems More on creep testing machines
Various liquid fuels used for space launch systems have to be cooled down to cryogenic temperatures. Their selection depends on the specific requirements of the mission, the desired performance and the technological possibilities, including in the production of liquid fuels. With decades of experience in the development of space launch systems for the aerospace industry, experience has also been gathered when it comes to the behavior of various materials at cryogenic temperatures. However, this knowledge is not widely available and does not exist for new material systems. Furthermore, previously built rockets were designed for single launch purposes, while some current systems are designed for multiple launches and reusability. For future sustainable drive concepts in aviation, the longterm objective is to use liquid hydrogen, which must then be stored on board at -253 °C (20K).
The very long service life of modern commercial aircraft means that, in addition to the static material behavior at cryogenic temperatures, the fatigue behavior of the materials used to construct the onboard systems is now increasingly coming into focus. Previous findings on material behavior at cryogenic temperatures from past space travel can therefore only be applied to future developments in the field of aviation to a limited extent.
ZwickRoell offers static and dynamic testing solutions forcryogenic test methods used in the material characterization of metallic materials as well as unreinforced and fiber-reinforced plastics. Depending on the cryogenic temperatures to be reached, a choice is made between immersion cryostats (77K) or continuous flow cryostats (ambient temperature up to 15K).
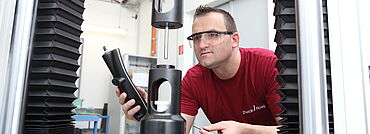
In addition to the mechanical properties of the materials used in aerospace structures, the structural behavior is largely determined by the properties of the various bolt and rivet connections used. For this purpose, the static strength and, in particular the fatigue strength of the mechanical fasteners implemented in these structures, must be tested using dynamic tests—especially those defined in the standardized test methods according to ASTM F606 and NASM 1312-8 and NASM 1312-13.
ZwickRoell offers static and dynamic testing solutions for reliable and efficient performance of these types of tests.
Metallic parts and components for aerospace applications and defense technology are subject to the highest demands in terms of reliability, service life and functional integrity, sometimes under extreme operating conditions. With the safe-life design principle used in the aerospace industry, for example, failure or malfunction of a component designed under these guidelines is ruled out during its intended service life. Metal components are therefore subjected to close process monitoring and precise quality control methods. Hardness testing also plays an important role in these situations.
ZwickRoell offers hardness testing machines that meet all established hardness test methods and international test standards.
More on the hardness test methods More on hardness testing machines