Testing of tire components
The following tests, among others, are performed at ambient and typical environmental temperatures from -70 to +250 °C:
- Tensile and tear growth test on elastomers with various specimen shapes
- Hardness, rebound, and abrasion tests on elastomers
- Abrasion tests on steel and textile cords made of elastomer bearings
- Tensile tests on steel- and textile cords Automated specimen feeding due to the large specimen quantities during the development of new compounds
- Determination of viscoelastic properties
Testing of wheels
In the automotive sector, wheels are made of steel, light metal, or composite materials and their tires. Tires are complex composite bodies composed of materials with various physical properties. As the link between the roadway and the vehicle, they transfer all forces and torques. ZwickRoell testing systems are used to determine the quasi-static and dynamic properties of wheels and tires. This ranges from standard tests on rubber, textiles, and wires to tests on the entire wheel/tire system.
Testing of tires and wheels
The stiffness of automobile tires is determined by measuring the force ratios under vertical and horizontal loads as well as variable tire pressure. For this, we would use a 50 kN AllroundLine materials testing machine with a horizontal linear unit and a multi-component force measuring platform on the lower base crosshead. Using the respective test program within the testXpert testing software, you can perform the desired tests under vertical and horizontal load application with varied tire pressure and then evaluate them.
Testing axial deformations of the rim flange
To determine stiffness properties, compression tests are performed on the rim flange with a special pressure spindle. For this, a floor-standing testing machine with a forward projecting, height-adjustable T-slot crosshead is used. This way the rims can and be positioned at an ergonomically comfortable height in the test area and be affixed. The load cell ensures exact measurement of the axial force, even if lateral forces occur due to the geometric shape of the rim. Due to its special construction and placement, the load cell can be inserted into the upper and lower test area of the machine for measurements.
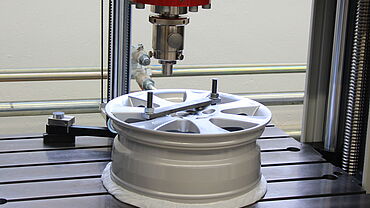
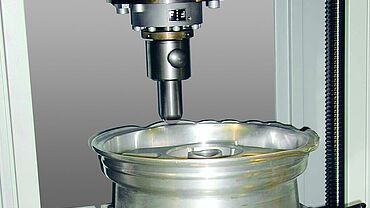
Determination of full-surface deformations on lightweight rim
The axial or radial axle load is variably applied through an electromechanical actuator and the deformation behavior is recorded via an optical 3D deformation measuring system. The strain results provide information about possible weak points in the component.
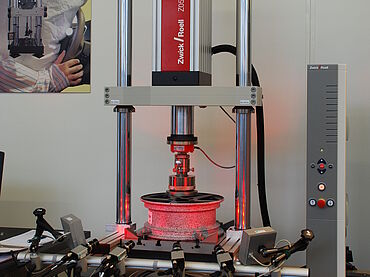
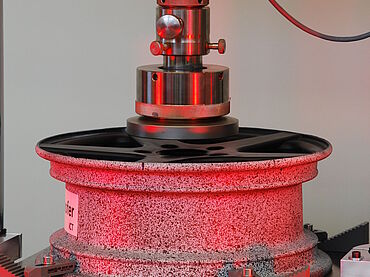
Hardness test on flanges
For steel and aluminum rims, hardness tests are primarily performed according to the Brinell method HBW 2.5 or using Rockwell tests (e.g., HRB) for production control purposes and also to ensure strength characteristic values. In addition, loads of up to 250 kg can be performed using closed loop controlled technology for all classic hardness test methods (Brinell, Rockwell, Vickers, Knoop, and ball indentation hardness) for metal and plastic applications. Even large components can be easily accommodated in the 250 x 300 mm (D x H) test area.
Testing of disc brake pads
Disc brake pads are one of the most important parts of a wheel brake. In order to evaluate the quality of the pads, you determine, among other things, the change in pad thickness through one dimensional compression loading in the direction of the disc brake pad's friction surface perpendiculars.
To handle this task, ZwickRoell materials testing machines are equipped with a compression test kit featuring an integrated measuring system. The deformation is measured via three measuring transducers that are positioned at a 120° offset on a pitch circle. Pressure is applied via an adapted piston replacement compression piece with circular force application. The compression piece's flexible suspension assembly allows exact parallel placement on the disc brake pad, ensuring a completely uniform and homogeneous application of pressure. The testing position of the compression die runs through the center axis of the disc brake pad's center of area. The test kit is suitable for both one-piece and divided disc brake pads.