Testing of Connecting Rods
Fatigue tests on connecting rods: The load collective acting on connecting rods requires a design (including the materials used) that meets the demands placed on it. The fatigue limit of connecting rods is assumed to be approx. N = 5 x 106 cycles. The connecting rod can be divided into three load areas. Both eyes must be tested under real conditions, that is with play and in a temperature range of 90 – 120 °C surrounded by oil. ZwickRoell's Vibrophore with special forked specimen grips allows you to achieve a testing frequency of up to 250 Hz. High specimen throughput and low energy consumption mean correspondingly low operating costs.

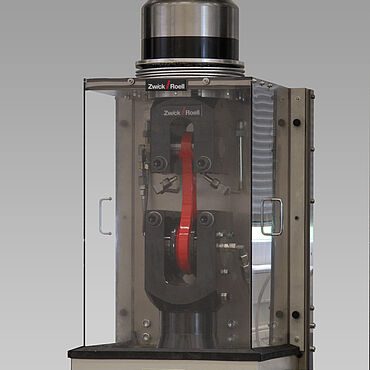
Testing of crankshafts
For fatigue testing on crankshafts, you can use a Vibrophore or a servo-hydraulic testing machine. In the case shown, the S-N curve is determined to DIN 50100. Due to the relatively low frequency of 10 to 30 Hz, a servo-hydraulic testing machine was used. Fatigue occurs through flexural loading in which the mounting table and tools are arranged so that all of the crankshaft's segments can be checked by reclamping them. A fatigue limit of approximately N = 3 x 106 cycles is assumed here. Force-controlled sinusoidal cycles are performed according to the staircase method. Fatigue testing via torsional loading can also be performed using the same machine.
Testing of valve springs
The combination of ZwickRoell’s precision spring compression test kit with the zwickiLine single-column testing machine (zwickiLine) and testControl II electronics create the ideal spring testing machine. The kit is extremely transverse force-resistant and protects against overload. The grounded, demagnetized compression platens have a parallel alignment accuracy of 1 μm / 10mm and precision guides permit only precise vertical movement of the compression platens. Measuring errors caused by deformation or lateral forces of the springs are reduced to a minimum thanks to the extremely stiff load cell, which is resistant to transverse forces. The corresponding testXpert test program is specially designed for tests of this nature, and the precision spring compression test kit offers exceptional capabilities in spring testing.
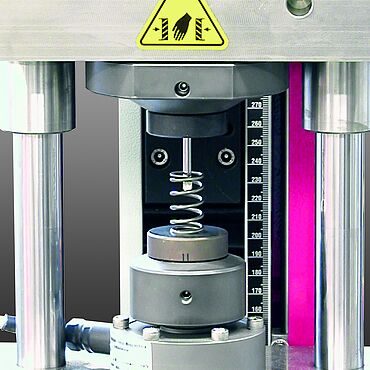
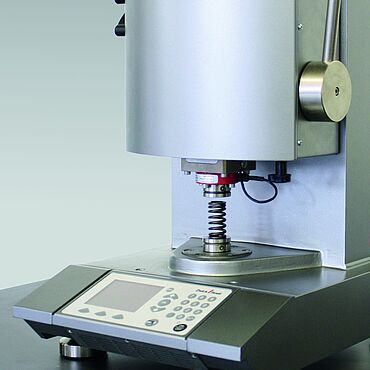
Testing of valves
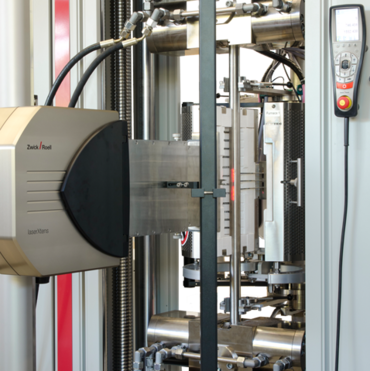
High temperature testing on valves
Testing of the engine block
Combustion engines consist of the three main components: the engine block (cylinder housing), crankshaft drive, and timing assembly. The cylinder block can be made up of just one unit or individual cylinders. It consists of one or several castings, in which cast iron, or increasingly also lightweight metal, for example, aluminum or light metal alloys of aluminum/magnesium are used. The cylinder block is subject to many loads, such as moments of inertia, torque, or forces from the transmission of the gas forces from the cylinder head to the crankshaft bearings.
Testing of timing chains
Vibrophores are available to help determine the fatigue properties of individual chain components in series production. The fatigue properties and limits of endless chains as well as individual chain components (for example, chain bridges) can be determined with a testing frequency of up to 50 Hz. ZwickRoell's control electronics were developed specifically for chain testing and allow you to even measure chains with large changes in damping. They can also be readily adapted to company-specific testing standards.
Testing of fuel injectors
The ZHN universal nanomechanical tester is used for comprehensive, mechanical characterization of thin layers or small surface areas with the necessary force and travel resolution. This includes measuring indentation hardness, indentation modulus, and Martens hardness to ISO 14577.
Testing of camshafts
Because of how they are used, camshafts must withstand high, continuous torsional loads. Torsion testing machines can be used for production-related quality control. The torque acting on a camshaft at which component connections begin to loosen is determined. Camshaft sections are gripped horizontally in the machine and a torque load of up to 1000 Nm is increasingly applied. Especially interesting is the elastic and plastic deformation of the camshaft components. ZwickRoell's optical laser extensometer measures the rotational angle without making contact.
Tests under high temperature
In applications such as engine design, power plant design, powertrains, and chemical plants, the material behavior under increased temperatures up to approx. 1,600 °C and higher are of vital importance. Tensile tests are primarily performed for these applications under increased temperature, although flexure tests are as well.