ISO 527-4 | ISO 527-5 Tensile Testing of Fiber-Reinforced Composites
The tensile test according to ISO 527-4 and ISO 527-5 is used to determine the tensile modulus and Poisson’s ratio elastic characteristic values, as well as the tensile strength in the main material directions of fiber-reinforced plastics. ISO 527-4 describes the test conditions for isotropic and anisotropic fiber-reinforced plastics. This includes composite materials with non-unidirectional reinforcements, such as mats, wovens or cut fibers, as well as multi-directional laminates made of unidirectional individual layers. ISO 527-5 describes the test conditions for unidirectional (UD) fiber-reinforced plastics. Both standards refer to ISO 527-1 for general principles for the determination of tensile properties.
Another frequently used standard for tensile testing of long or continuous fiber reinforced plastics is ASTM D3039, which includes the test conditions for isotropic and anisotropic fiber-reinforced plastics, as well as for unidirectional fiber-reinforced plastics.
Objective and characteristic values Video Running a test & test equipment Test conditions Specimens & dimensions Additional information Downloads
Test objective and characteristic values to ISO 527-4 and ISO 527-5
Tensile tests for fiber-reinforced plastics are performed to determine tensile properties in the material development and qualification process, for the determination of characteristic values to be used for the layout and design of composite structures, as well as in quality assurance. Regardless of the type of fiber reinforcement, the following characteristic results and characteristic values are determined in ISO 527-4 and ISO 527-5:
- Tensile stress: force related to the initial cross section of the specimen
- Axial strain: change in gauge length with reference to the initial gauge length in load direction
- Transverse strain: Change in the gauge length with reference to the initial gauge length in transverse direction (only necessary for determination of the Poisson’s ratio)
- Tensile modulus: slope of the stress-strain curve in a specified strain interval in the elastic range. Also called modulus of elasticity or Young’s modulus
- Tensile strength: maximum value of the tensile stress determined in the tensile test
- Strain at break: axial strain when tensile strength is reached
- Poisson's ratio: negative ratio of transverse strain to axial strain
ISO 527-4, ISO 527-5, as well as ASTM D3039 establish the test conditions for tensile testing of fiber-reinforced plastics. Despite the similarities in the test methods, the determined characteristic values are not fully comparable, since the specimen shapes and specimen dimensions as well as the characteristic value determination differ in some aspects (e.g., strain interval for the tensile modulus).
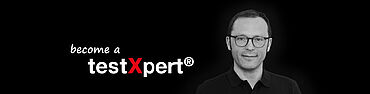
Reliable testing to ISO 527-4 and 527-5 with testing software testXpert
testXpert supports efficient testing and reliable test results to ISO 527-4 and ISO 527-5:
- Eliminate the need to study the standard: guaranteed standard compliance through standard test programs - all characteristic values and parameters specified by ISO 527-4 and ISO 527-5 are pre-configured.
- Maximum testing efficiency is achieved through the connection of peripheral devices: when the specimen dimensions from the micrometer are sent directly to the testing software, you save time and avoid input errors.
- Additionally, verify and control the temperature in the chamber via the software. Set temperature ramps and see the values that have been maintained retrospectively, with traceability.
Specimen grips and alignment fixture for reliable test results to ISO 527-4 and ISO 527-5
To perform the tensile test to ISO 527-4 and ISO 527-5, the corresponding tensile specimen is gripped in the specimen grips of a static testing machine. It is recommended to regularly check for correct specimen grip alignment according to ISO 23788 or ASTM E1012. For Nadcap accredited testing laboratories in the aerospace industry, alignment verification is mandatory. Mechanical body-over-wedge or hydraulic body-over-wedge grips are ideally suited for this requirement. If proof of alignment is not required, conditionally alignable wedge screw grips can also be used.
Tensile testing machines for ISO 527-4 and ISO 527-5
For tensile tests to ISO 527-4 and ISO 527-5 with standard specimens and for many other standardized test methods for fiber-reinforced plastics, use of a 100 kN testing machine is often sufficient. With the 100 kN machine configuration shown on the right, the use of mechanical body-over-wedge grips makes it easy to switch between different test arrangements and test fixtures. Because the specimen grips are easy to remove, the entire work area of the testing machine can also be used for non-standard tests. The support legs enable individual and ergonomic adjustment of the work area height.
If testing is performed exclusively on glass fiber-reinforced plastics (GFRP), a static machine with a maximum force of 50 kN is normally sufficient.
Modular testing system for composites
Larger testing laboratories with correspondingly high test volume use different testing machines for the very diverse composite testing methods, and can thereby minimize conversion efforts. The individual testing machines can be adjusted to the force range required for the various types of tests. If throughput rates are not high or consistent enough that an investment in multiple testing machines makes sense, an alternative option is to equip a single testing machine so that you can perform as many test methods as possible with the least amount of machine conversion effort.
ZwickRoell developed a modular design, which is available as a 100 kN or 250 kN testing machine covering 21 test methods and approximately 120 test standards (ISO, EN, ASTM, as well as Airbus AITM and Boeing BSS), and which allows for comprehensive characterization of fiber-reinforced composite materials at ambient temperature or for tests at low or high temperatures ranging from -80 °C to +360 °C.
Extensometers for strain measurements to ISO 527-4 and ISO 527-5
For correct determination of the elastic characteristic values and strain at break, it is necessary to measure strain directly on the specimen. To determine the Young's modulus and strain at break, measurement of the axial strain is sufficient. To additionally determine Poisson’s ratio, a biaxial strain measurement system is required, which also allows you to measure transverse strain. For the strain measurement you can use strain gauges, sensor-arm measuring systems such as clip-on extensometers (limitation: not up to specimen break) or automatic sensor arm extensometers (makroXtens, multiXtens) as well as non-contact optical systems (videoXtens).
Test conditions a test to ISO 527-4 and ISO 527-5
Test speed
The constant test speed to be set depends on the specimen type and the purpose of the test. Higher speeds can be set for tensile tests for quality control purposes than for tensile tests used for material characterization.
- Valid specimen failure
Specimens that break within the jaws or in the transitional area from jaw to ungripped area of the specimen are invalid and must be replaced with a new specimen to achieve at least five valid test results.
Temperature range
Since the mechanical properties of fiber-reinforced plastics can be largely temperature dependent, in addition to tensile tests at ambient temperature, tests are also performed at low and elevated temperatures. Here, the testing machine can be equipped with a temperature chamber for a temperature range of -80 °C to 360 °C.
Specimens and dimensions to ISO 527-4/527-5
- l = Total length of the specimen
- L = Span between the jaws of the specimen grips
- b = Width of the specimen
- h = Thickness of the FRP laminate
- L0 = Recommended gauge length for extensometers (sensor arm or non-contact): ISO 527-4 specimen type 4 L0 = 25 mm, for all other specimen types listed above L0 = 50 mm
Standard | Specimen type | Schematic diagram (simplified, not to scale) | Application |
---|---|---|---|
ISO 527-4 | Type 1B Dumbbell | ![]() |
|
Type 2 Rectangular without cap strips | ![]() |
| |
Type 3 * Rectangular with cap strips | ![]() |
| |
Type 4** Conical without cap strips | ![]() |
| |
ISO 527-5 | Type A, type B *** | ![]() |
|
- * For specimen type 3 in ISO 527-4 and specimens type A and B in ISO 527-5, cap strips are applied to both sides of the specimen. The objective of these force application elements, which are usually bonded to the laminate to be tested, is to reduce stress concentrations in the grip so that jaw breaks (breakage at or in the jaws of the specimen grips) are avoided. For this purpose, cap strips made of ±45° GFRP laminate have proven their worth. Straight cap strips are always used, whereas ASTM D3039 also allows the use of cap strips with scarf angles. Other force application elements, including those that are not bonded, can be used (e.g. abrasive cloth or sandpaper) provided that it can be demonstrated that the same strengths are achieved and that there is no major scatter in the characteristic values.
- ** For specimen type 4, newly included as of ISO 527-4:2023, which is intended for tensile testing without cap strips on multidirectional continuous fiber-reinforced thermoplastics, the results must be recalculated if the break occurs outside the L0 = 25 mm straight gauge length in the specimen center. The fracture-related calculation of the tensile strength for specimen type 4 listed in ISO 527-4 Annex E is already included in the pre-configured testXpert test program for ISO 527-4:2023.
- *** Specimen types A and B in ISO 527-5 feature different laminate thicknesses and specimen widths. Specimen type A, intended for the tensile test in 0° direction of a UD laminate, has a width of 15 mm and a laminate thickness of 1 mm. Type B, on the other hand, intended for the tensile test in 90° direction of a UD laminate, has a width of 25 mm and a laminate thickness of 2 mm. This ensures that the forces measured in the 0° tensile test are not too high and the forces measured in the 90° tensile test are large enough and thus both specimen types can be tested using the same test arrangement. This geometric adjustment is necessary because ID laminates exhibit extreme differences in strength in the direction of the fibers and across the fibers.
More information on ISO 527-4 & ISO 527-5
- To determine tensile properties at the single-layer level, multilayer composites are produced in which each individual layer is oriented in the same way. These include the 0° or 90° UD laminates designated in ISO 527-5. In the case of correspondingly oriented multilayer woven composites in ISO 527-4, mechanical characteristic values are also referenced in terms of warp and weft direction.
- In addition to performing tensile tests for material development, material qualification and quality assurance purposes, the characteristic values determined at the single-layer level are also used in the design of composite structures for analytical calculation methods. Using the classical laminate theory, for example, the elastic properties of a multidirectional multilayer composite can be calculated from the characteristic values of the respective individual layers. The strength values at the single-layer level are used, among other things, for the calculation of failure criteria such as maximum stress, Hashin, Puck or LaRC.
- Since the mechanical properties of a multilayer composite depend on the orientation of the respective individual layers, every multilayer composite with different individual-layer orientations presents different mechanical tensile properties. The mechanical material properties of fiber-reinforced plastics therefore only come to light during the manufacturing process of the laminate. The manufacturing process itself has a significant influence on the resulting characteristic values. The influence of the manufacturing process on the mechanical properties of a fiber-reinforced plastic (FRP) laminate is therefore often validated by mechanical testing.