Autoclave: Materials Testing in Compressed Hydrogen Environments
Tests in a compressed hydrogen environment are of high significance in the field of material research and development. With the use of an autoclave materials can be qualified under high pressure, at both high and low temperatures. This is particularly important in the development of new materials for use in highly stressed applications.
The use of compressed hydrogen presents a particular challenge for testing technology. Hydrogen, when combined with atmospheric oxygen, forms an explosive mixture known as oxyhydrogen. It is therefore important to carefully plan all testing systems that work with compressed hydrogen and design them in accordance with the applicable safety regulations.
Autoclave operating principle Tests in compressed hydrogen autoclave Video Safety & maintenance Testing systems Interesting customer projects
Operating principle of the autoclave
- An autoclave is a closed, gas-tight pressure vessel.
- Autoclave technology is well known in the field of steam sterilization of food products, the medical industry and in manufacturing of fiber-reinforced composites.
- For hydrogen testing in a compressed hydrogen environment, the test is carried out in an autoclave by adding compressed hydrogen. This simulates the stresses to which the materials are subjected when used for their intended application.
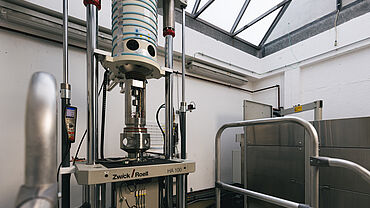
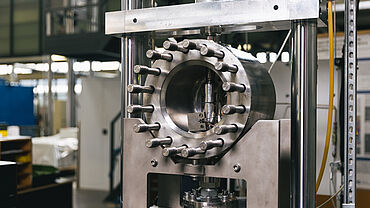
Testing in compressed hydrogen autoclaves
ZwickRoell autoclaves are specially designed to test materials in compressed hydrogen environments. The autoclave takes on the task of the pressure vessel in which the hydrogen acts on the specimen surface under pressure and penetrates it. In addition to the mechanical loading of the specimen by the machine, the mechanical properties of the specimen are determined under the influence of hydrogen.
With the resulting material characteristics, we can determine the material’s hydrogen resistance. This can then be used for the development of new hydrogen-resistant materials and to investigate existing materials for use with hydrogen.
- Compressed hydrogen tanks or vessels (autoclaves) installed in a servohydraulic testing machine can be used to perform a variety of tests including fracture toughness tests (ASTM E1820, ASTM E399, BS 8571, ASTM E647, ISO 11114-4), fatigue tests and slow strain rate tests on threaded-end specimens, notched specimens and CT specimens. In addition, this testing system can be used for static tests, including tensile tests and flexure tests in a compressed hydrogen environment.
- When installed in a creep testing machine, the autoclave can be used to perform the above-mentioned cyclic tests at frequencies < 2 Hz, as well as creep-fatigue tests (ASTM E2714, ASTM, E2760). Static tests such as tensile tests and slow strain rate tests (ASTM G129, ASTM G142), in particular, are performed with the highest precision.
- Standard hydrogen tanks up to 400 bar are integrated in the testing machines. These were specially developed by ZwickRoell for use in materials testing and are particularly optimized in terms of alignment, pressure compensation and force measurement. Special versions are available for up to 1,000 bar. The compressed hydrogen is prepared using a hydrogen compressor. The testing machine is equipped with a 40 l/min hydraulic power pack.
Testing in compressed hydrogen autoclaves: Safety and maintenance
- To ensure safety when using compressed hydrogen in autoclaves, strict safety guidelines must be met.
- This includes, for example, regular checking and maintenance of the systems, the use of safety equipment and devices, as well as proper training of employees on safe work practices.