Testing of metallic hollow specimens under compressed hydrogen
Low investment and testing costs, fewer safety measures, and easy to operate: These are the benefits of testing metallic hollow specimens under compressed hydrogen to determine the influence of hydrogen embrittlement. This alternative method to autoclave technology, for the qualification of materials under compressed hydrogen, is ideal for tensile tests, creep tests and tests with alternating loads.
Operating principle of the hollow specimen method Video Advantages Retrofitting TransHyDE – H2 Transport research project FAQs Related testing machines
Operating principle of the hollow specimen method
From specimen preparation to the start of the hollow specimen test in just a few minutes:
- The hollow specimen is safely filled with pressurized hydrogen outside the laboratory. The internal pressure can be up to 200 bar.
- The hollow specimen is then transported to the lab and inserted in the specimen grips.
- The extensometer is attached to the hollow specimen for strain measurement and control.
- The standard compliant test program is loaded and the test is started in testXpert.
Benefits of the hollow specimen technology at a glance
- Ideal for tensile tests, creep tests, slow strain rate (SSRT) creep tests and tests with alternating load up to max. 2 Hz.
- Significantly lower investment and testing costs.
- Simple operation and handling.
- The specimens can be filled with a wide variety of gases and mixtures, such as hydrogen, natural gas and nitrogen.
- Few required safety measures; the hollow specimen test can be carried out in a normal laboratory environment. We will advise you on the necessary explosion protection documents.
- The hollow specimen technology is ready to be retrofitted on existing testing machines.
Low security measures
The hollow specimen test can be carried out in a normal laboratory environment without the need for complex safety measures.
- The hollow specimen technique only requires approx. 0.1% hydrogen volume compared to the autoclave technique.
- The hollow specimen is safely filled with pressurized hydrogen outside the laboratory.
- All sensors in potentially explosive atmospheres comply with the Atex Directive 2014/34/EU.
- We are here to advise you on the necessary explosion protection documents and will help guide you as necessary.
Low investment and testing costs
Compared to autoclave technology, the investment and testing costs required for the hollow specimen technology are significantly lower. Why? For one, the test arrangement is less complex, and on the other hand, the reduced safety measures eliminate the high costs associated with complex safety precautions and retrofit work in the laboratory. The lower hydrogen consumption and shorter test times for hollow specimen testing also reduce continuous testing costs.
Hollow specimen and autoclave technology in comparison
Hollow specimen | Autoclave | |
---|---|---|
Advantages |
|
|
Disadvantages |
|
|
Retrofit the hollow specimen technology onto your existing testing machine!
The H2 hollow specimen technology can be retrofitted to ZwickRoell and third party testing machines. Overview of applicable testing machines from ZwickRoell:
- Electromechanical creep testing machines: Kappa DS, Kappa SS and Kappa SS-CF
- Electromechanical testing machines, including the AllroundLine, tensile tester for large test forces
- High-temperature testing systems for which the high-temperature furnace or the temperature chamber can be swiveled out completely from the test area.
- Servohydraulic testing machines (ideal for static or quasi-static tests up to max. 2 Hz on hollow specimens)
To retrofit your existing equipment, our specialists will first check the suitability of your testing machine. Please contact us. We are here to discuss your needs and find the right solution.
Hollow specimen test: collaboration in TransHyDE – H2 Transport research project
The development of the method incorporates the results of initiatives and projects related to hydrogen, in which ZwickRoell is also involved:
To validate the reliability of the method and ensure regulatory safety for future customers, we at ZwickRoell are working alongside partners from the areas of research and industry within the TransHyDE project of the German Federal Ministry of Education and Research (BMBF) to lay the foundations for standardization. ZwickRoell is involved in the TransHyDE – H2 Transport project, which is developing and assessing various technologies for hydrogen transport and evaluating the possibilities of hollow specimen testing as an alternative to autoclave technology. In addition, the project will evaluate the effect of specimen geometry and surface area through the drilling method and investigate the effect of gas purity on specimens. We are also actively working on the definition of the international test standard ISO/TC 164/SC 1/WG9 in the TransHyDE – H2 Transport associated sub-project H2 HollowTensile (H2HohlZug), which addresses the standardization of hollow tensile specimen technology.
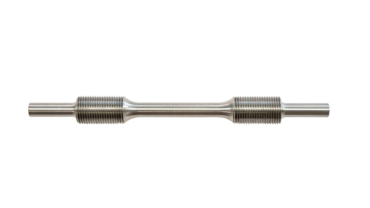
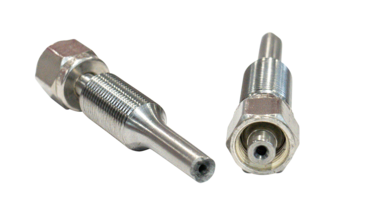
FAQs - Frequently asked customer questions
The hollow specimen technique is Ideal for tensile tests, creep tests, slow strain rate (SSRT) creep tests and tests with alternating load up to max. 2 Hz. Internal pressure can go up to 200 bar during a hollow specimen test.
The hollow specimen technique is used to test metallic materials under pressurized hydrogen.
The hollow specimen can be filled with different gases and mixtures. Most tests are carried out with hydrogen, but testing with natural gas and inert gases such as nitrogen is also possible.
In this test method, the volume of hydrogen in the hollow specimen is only a fraction of the volume of hydrogen used in an autoclave (only 0.1%). Even after the end of the test or in the event of specimen breakage, only a small amount of hydrogen escapes from the testing lab and evaporated immediately.
We are here to advise you on the necessary explosion protection documents and will help guide you as necessary.