Durability
Durability is a term used in materials science, which refers to the calculated service life of a component. Durability describes the ability of materials and components to withstand static, quasi-static and dynamic (recurring or impact) loads without damage, within the calculated service life and under consideration of relevant environmental conditions.
Methods for durability determination can be either calculated methods or test results. Durability is therefore a cross-sectional science consisting of the interaction of load (mechanical and environmental), material, production and construction.
Dynamic stresses are almost invariably the cause of component failure. Often the failure occurs with loads that are significantly below the failure load observed in static tensile tests. Fatigue life, as part of the durability, designates the deformation and failure behavior of materials under cyclic stress.
The number of cycles that a component can withstand under operating load until failure can be predicted with statistical accuracy using the S-N curve.
Durability of a component Experimental determination Simulation tests Standardized load sequences Testing machines
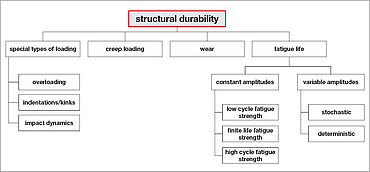
Durability of a Component
Many times developers do not design a component to be fatigue resistant, but rather to exhibit high durability.
For determination of the durability of a component, all types of loading must be considered—from static creep loading to impact loading to cyclic loading, at constant or variable amplitude. Environmental conditions such as temperature, precipitation, pressure, as well as changes in the material due to corrosion or aging are taken into consideration. The challenge then is to determine characteristic values using the simplest possible tests, on the basis of which the designer can develop a reliable component.
The problem here is that the damage process is highly complex and cannot actually be described by a single parameter. It always begins with the formation of micro-cracks emanating from internal flaws or notches at which cyclic plastic deformations occur. The LCF test is used in the attempt to describe this process. This is followed by crack growth up to failure, for which the methods of fracture mechanics are used.
The high cycle fatigue test (also S-N test) makes no distinction between crack initiation and crack growth. Using the S-N curve, it is relatively easy to predict service life at variable loading amplitudes by means of damage accumulation methods (e.g. Plamgren/Miner).
However, there is still the component test for verification, although this involves significantly less effort thanks to modern methods of material characterization.
Today, durability is tested in almost all technical fields. Durability offers certain advantages, particularly in lightweight construction. Components require less material and therefore have a lower mass when they are designed to be durable rather than fatigue resistant. In the automotive industry, for example, a lighter vehicle requires less fuel, but the lighter structure also allows a higher load capacity. Durable design in part also fulfills a functional requirement: airplanes designed to be fatigue resistant would not be able to fly since they would simply be too heavy.
Development of a Component
During its operation, almost every component of a machine, system or vehicle is exposed to mechanical loads that cause change over time. The task for developers is to create a product that fulfills its function over its entire service life. This is often contrasted by short development times, demands for lightweight construction and cost-effective production. The application of calculated service life estimation in fatigue testing supports the reliable and economical design of components. Fatigue fracture mechanics additionally supports the description of crack growth. Characteristic numbers from the non-destructive test can be included in product development.
The goal for a durable component is
- Achievement of the required service life
- Reliability of components that make up a structure or an entire system
- The assurance against failure or downtime before reaching the rated service life (probability of failure)
Experimental Determination of Durability
The service life of a component is not only dependent on the level of the load, but also on the load sequence. In the case of durable component design, operation-similar load-time sequences (load sequences with variable amplitude) provide more reliable information about the service life than tests with monotonous loading.
Simulation Tests
To test durability, simulation tests are performed where a recorded load-time signal is to be reproduced as accurately as possible on the test bench. The behavior of the test bench and component leads to the fact that the actual signal, despite an optimally set controller, does not correspond with the desired set-value signal. In order to improve the simulation behavior (correspondence between the set-value or target signal and the actual signal), the set-value signal is changed in an iterative process until the actual signal corresponds with the original set-value signal.
Related Products for the Determination of Durability
Different materials and components require implementation of different testing technologies. In the last several years, ZwickRoell has therefore made tremendous investments in the development of dynamic testing machines and drive technologies and now offers the right drive concept for any testing application:
- Electromechanical testing actuators provide a modular concept for low frequencies up to 1Hz and 50 kN
- The LTM linear testing machines are part of an electrodynamic testing machine series featuring a drive based on linear motor technology. The drive was specially developed for testing technology and is patented by ZwickRoell
- The vibrophore series resonance testing machines offer very high testing frequencies at very low operating costs. Testing frequencies up to 285 Hz can be reached.
- The servohydraulic testing machines with standardized load frame design provide maximum flexibility for any application
With this wide variety of drive technologies, ZwickRoell is the only testing machine manufacturer able to provide neutral advice on the best drive concept for your applications. All of the different machines use the same testing software and control technology. This minimizes training efforts for everyday laboratory tasks.
The above mentioned machines can be used as , which is made possible by the combined use of our testControl II electronics and proven testXpert testing software.
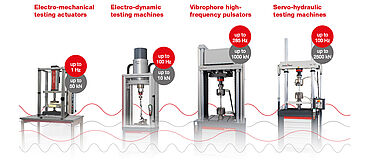