Critical aspects for sustainable implementation and testing of injection systems
Based on our many years of experience in introducing testing processes and testing solutions, we have determined four critical aspects that facilitate the implementation of injection systems and create sustainable, effective processes for testing injection systems.
4 Critical Aspects for the Sustainable Implementation and Testing of Injection Systems
Choose clever solutions
This allows you to minimize risk and reach your goals faster.
Decrease efforts
Speed up the planning phase with our off-the-shelf URS templates and qualification packages for DQ, IQ, OQ.
Minimize errors, maximize output
Our fail safe design ensures smooth processes and prevents unnecessary errors.
Optimize system uptime
To keep your tests running.
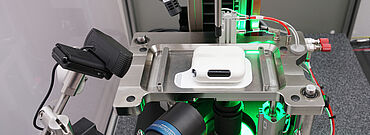
What proven and intelligent testing systems can do
The responsibility towards your customers is immense. Minimize risks and rely on our tried and tested solutions that are founded on many years of experience and are designed to avoid potential errors and help you reach your goals quickly. Here are a few examples:
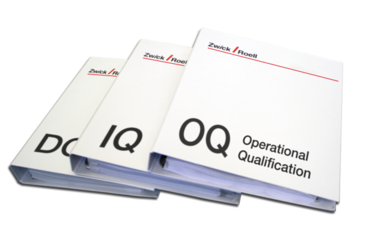
Decrease efforts: use URS templates and qualification packages for DQ, IQ, OQ and save valuable time
To support you during your planning phase, we have put our experiences down on paper. For your user requirement specifications (URS), you will receive a complete specification sheet from us, where you can go through the individual points step by step to ensure that nothing is overlooked. This is a service for which our existing customers continuously sing their praises. It guarantees that you are always on the safe side and saves valuable time.
This also simplifies the qualification process, because the URS specifications contain the invaluable experience of our qualification team. With the special packages for design qualification (DQ), installation qualification (IQ) and operational qualification (OQ), you are in excellent hands.
We’re with you all the way, from the URS through qualification.
When it comes to traceability, we’ve got it covered: our white paper provides assistance and answers all the important questions regarding FDA 21 CFR Part 11.
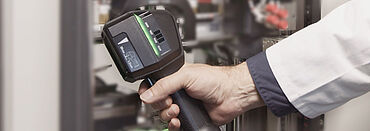
Fail safe design: minimize errors, maximize output
Fail safe design ensures smooth processes and helps you avoid unnecessary errors. A defective sensor, an improper or incorrectly placed injector, or wrong change parts – all these are errors that can be avoided.
The following components prevent unnecessary costs and ensure that batches are reliably released:
Daily Check
To recheck the proper run of the test relevant sensors on a daily basis, we have a full range of Daily Check tools and software.
- Daily Check for load cell
- Daily Check laser sensor
- Daily Check for camera based measuring systems
- Daily Check for scale
- Daily Check for microphone
- Daily Check for color sensors
- Customized Daily Check solutions
Vision sensor
The vision sensor ensures that the correct test specimen is used and that it is inserted in the correct orientation. To do this, the sensor detects colors, shapes, and edges to also ensure that the correct injector has been inserted. The vision sensor detects user errors and alerts you if something is wrong.
Repeatable test conditions
If you use your testing machine for different injection system tests, our testXpert testing software guarantees automatically repeatable test conditions after the application and testing fixtures have been changed. The settings and parameters are loaded automatically, and you can start testing right away. The software also protects the sensors against overload and damage.
Fast, standard compliant and cost efficient testing of PFS (prefilled syringes)
For the latest OndrugDelivery magazine edition, ZwickRoell contributed valuable information for systematic increase in productivity in the testing lab using different testing solutions for prefilled syringes. Take a look!
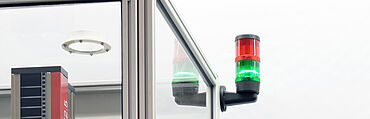
Optimize system uptime
Ensuring high machine availability avoids unwanted costs. The outstanding product quality of our testing machines and components is already a very good foundation for this, and the documentation for machine downtimes provides assistance in an emergency.
We also offer options that allow you to increase machine availability even further:
- customized spare parts packages for immediate repairs on site
- Service response packages
- Customized training for your employees
We will advise you on the right options so that you are prepared in an emergency and put together the right package for your needs. We look forward to working with you and supporting you with your testing requirements. Let's talk!