ISO 8295: Coefficient of Friction
Among other things, the coefficient of friction (COF) provides information about the surface texture and printability of plastic films. The static and kinetic coefficient of friction is particularly interesting for films that are further processed on packaging and printing machines. It also plays an important role in EV battery testing in the form of separator films.
The determination of the coefficient of friction of plastic films is described in standards ISO 8295, ASTM D1894, JIS K7125 and DIN 53375 (withdrawn).
Objective and applications Test results Specimens & dimensions Running a test & test equipment Coefficient of friction separator films Downloads FAQs Request a consultation
Objective and applications of the ISO 8295 standard
Determining the coefficient of friction in accordance with ISO 8295 is particularly significant for film materials that are further processed on packaging and printing machines. The coefficient of friction of plastic films, in particular the static and kinetic friction, provides information on the processability of the surface texture, which in turn is important for printing purposes. They are also important components of more complex products such as batteries for electric vehicles.
In ISO 8295, in addition to the typical film against film pairing, other combinations such as film against metal, film against glass, or two different types of film materials can be evaluated using the same test methodology. As a rule, however, the films used for this test are identical so that the sliding processes of a film stack or a film roll can be evaluated.
Characteristic values / test results according to ISO 8295
The coefficient of friction (μ) is the main result when testing according to ISO 8295. It indicates how well two materials move against each other or how easily they stick to each other. The coefficient of friction is described both as coefficient of sliding (kinetic friction) and starting friction (static friction). The higher the coefficient of friction, the rougher the surface of the material.
Static coefficient of friction μS = Fs/FP
Dynamic coefficient of friction μD = FD/FP
Abbreviation | Unit | Name | Short description |
μs | Static coefficient of friction |
| |
Fs | N | Static frictional force | F s is the static frictional force, expressed in Newtons |
FP | N | Standard force | FP is the standard force exerted by the mass of the carriage, expressed in Newtons (= 1.96 N) |
µD | Kinetic coefficient of friction |
| |
FD | N | Kinetic frictional force | FD is the dynamic frictional force, expressed in Newtons |
ISO 8295 test performance & test equipment
COF tester and test fixture:
- The test to determine the coefficient of friction according to ISO 8295 can be easily performed on a static zwickiLine testing machine with an additional ZwickRoell test fixture.
- The test fixture consists of a horizontal test table and a sled with known mass. The fixture can be used to determine the friction behavior between film and film as well as between film and sheet material made of stainless steel or glass.
Running a test:
- Film is clamped on the sled. A second film can be clamped to the stainless steel test table or onto the included glass plate, which is placed on the stainless steel table. The film pair is mounted between the table and the sled in such a way that there is full-surface support with evenly distributed pressure on the entire known surface area. This is accomplished by using a layer of felt.
- For the test, it is irrelevant whether the sled is moved across the table, or whether the movement stems from the table.
- To determine static friction, the sled is connected to the force sensor via a standardized tension spring with a fixed spring rate and a thread. This way, the tensile force on the sled can be accurately measured during the movement. Stick-slip effects should not occur in the measurement of kinetic friction, which is why a tension spring in not used.
Calculating the coefficient of friction:
- The coefficient of friction is presented as the quotient of the tensile force measured on the sled and the contact force of the sled that results from its own weight: Coefficient of friction μ = Fs/FD
- The static coefficient of friction (static friction) is calculated from the initial peak value of the tensile force on the sled, while the kinetic coefficient of friction (sliding friction) is calculated from the average value of the tensile force on the sled during a specified sliding distance.
ISO 8295 frictional properties of separator films in battery testing
In a lithium-ion battery, separator film separates the anode and cathode from each other to prevent electrical short circuits. At the same time, the separator allows the flow of ionized charge carriers that are needed to close the circuit in an electrochemical cell.
In addition to ceramic separators and glass fiber nonwovens, polymer membranes are primarily used. Determination of the tensile strength and strain at break provides information about the integrity of the separator film under operational mechanical stress. Thicker separator films efficiently and safely prevent contact between the anode and cathode, while thinner films make it possible to reduce the weight of the battery and improve the energy density.
The behavior of the separator with regard to the coefficient of friction between the electrode coating and the separator is also an important aspect. These characteristic values influence the performance of the cell and are particularly important for setting the production parameters in the winding processes. ZwickRoell enables tests at room temperature and, with the aid of ZwickRoell temperature chambers, tests at near-operating temperatures in the range of -20 °C to +50 °C. This ensures comprehensive characterization of the separator films under various conditions.
ISO 8295 and ASTM D1894 are often used as a substitute standard for characterizing their frictional properties, as there are currently no test standards specifically developed for EV batteries. The tests are also carried out in an electrolyte-wetted state in order to achieve realistic mechanical characteristics. Active involvement in the further development of these standards, especially for battery materials, ensures that ZwickRoell test methods will continue to meet all future requirements.
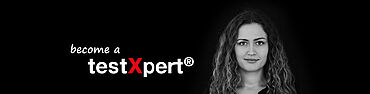
Take advantage of the leading testing software in materials testing
ZwickRoell’s testXpert testing software offers:
- Simple operation: start testing right away and be a testXpert while maintaining maximum safety.
- Reliable and efficient testing: benefit from reliable test results and maximum testing efficiency.
- Flexible integration: testXpert is the optimal solution for all of your applications and processes—simply put, a more effective workflow.
- Future-proof design: testing software for the entire life cycle, ready for your future test tasks!
Frequently asked questions about the determination of the coefficient of friction according to ISO 8295
The rougher a surface, the higher its coefficient of friction. It indicates how well two materials move against each other (kinetic, or dynamic friction) or how easily they stick to each other (static friction). The static coefficient of friction indicates how much force is required to move two materials, the kinetic or dynamic coefficient of friction describes the force that is necessary to keep them moving. The coefficient of friction (μ) is the main result when testing according to ISO 8295.
The coefficient of friction is calculated as the quotient of the tensile force measured on the sled and the contact force of the sled that results from its own weight. The formula for the calculation is:
- Static coefficient of friction: μS = Fs/FP
- Dynamic coefficient of friction: μD = FD/FP
where FS and FD are the static and dynamic frictional force (in Newtons) respectively and FP is the standard force exerted by the mass of the slide, expressed in Newtons (= 1.96 N).
ISO 8295 and ASTM D1894 are international standards for determining the coefficient of friction of plastic films. Among other things, the standards differentiate between the size and weight of the sled and the material with which the sled must be covered or sheathed. The size of the specimens also differs. In contrast to ASTM D1894, ISO 8295 specifies the use of a spring for the test.