ISO 527-1 & ISO 527-2 플라스틱 인장 시험
이 인장 시험은 몰딩 재료의 필수 기계적 성질을 측정하는 데 사용합니다. 이러한 물성값은 대부분 비교 목적으로 사용됩니다. 표준 ISO 527-1(일반 원칙)과 ISO 527-2(몰딩 및 압출 재료의 시험 조건)는 플라스틱 인장 시험을 설명합니다. ISO 527 표준의 지도 원칙은 시험실, 기업, 국경 간 시험 결과의 높은 재현성입니다.
플라스틱 인장 시험에 대한 자세한 사항은 ASTM D638 표준에서 확인할 수 있습니다.
목적과 물성값 시험 수행 시편 형태와 치수 환경 조건 정확도 요구사항 타 시험법과의 비교 시험 시스템 플라스틱 브로슈어
ISO 527에 따른 인장 시험의 목적과 물성값
몰딩 재료의 필수 기계적 성질을 설명하기 위해 일련의 물성값을 측정합니다. 이러한 물성값은 대부분 비교 목적으로 사용됩니다.
일반적인 물성값은 다음과 같습니다.
- 인장 응력: 초기 시편 단면과 관련된 힘
- 변형률: 초기 표점 거리와 관련한 표점 거리의 변화
- 인장 탄성률: 응력-변형 다이어그램 곡선의 기울기
- 항복점: 기울기가 0인 플롯 점의 응력과 변형
- 파괴점: 시편 파단 순간의 응력과 변형
- 푸아송 비: 축 변형률에 대한 횡변형의 네거티브 비율
ISO 527-1/-2 와 ASTM D638 은 모두 인장 시험의 시험 방법을 정의합니다. 이 두 표준 규격은 기술적으로는 동등하나 결과까지 유사하진 않습니다. 시편 형태, 시험 속도, 결과 해석 방법이 다소 다르기 때문입니다.
표준화된 인장 시험에서 결과는 시편의 정해진 시편 분리 속도를 바탕으로 합니다. 하지만, 실제 사용 중인 부품이나 구조에 가해지는 하중은 매우 광범위한 변형률 범위 내에 있을 수 있습니다. 폴리머의 점탄성 성질 때문에 변경된 변형률에서는 표준화된 시험 시편에서 측정된 것과 다른 기계적 성질이 일반적으로 발생합니다. 이런 이유로 인장 시험에서 측정된 물성값은 부품 설계에 대한 적합성이 제한적이지만, 매우 신뢰할 수 있는 재료 비교의 근거가 됩니다.
노화 시험
인장 시험은 노화, 열 또는 매체 노화, 풍화 이후 폴리머의 기계적 물성값 변화를 증명하기에 좋은 근거를 제공합니다. 이를 위해 인장 시험의 물성값은 정해진 노화나 풍화 기간 이후, 그리고 새로 성형된 상태에서 측정합니다.
ISO 527-1 인장 시험은 어떻게 이루어지나요?
testXpert III를 이용한 ISO 527에 따른 인장 시험 수행:
ZwickRoell의 testXpert III 시험 소프트웨어는 모든 시험 요구에 이상적인 솔루션입니다. 본 소프트웨어는 재료 물성시험 업계의 소프트웨어 사용자들과 긴밀하게 협업하여 얻은 결과물로, 일상 업무를 지원하는 기능을 다양하게 갖추고 있습니다. ISO 527-1/-2와 ASTM D638은 모두 인장 시험의 시험 방법을 정의합니다. 이 두 표준 규격은 기술적으로는 동등하나 결과까지 유사하진 않습니다. 시편 형태, 시험 속도, 결과 해석 방법이 다소 다르기 때문입니다. ZwickRoell은 testXpert를 통해 ISO 527-1 및 ASTM D638 요구사항 이행을 보장하는 준비된 표준 규격 시험 프로그램을 제공합니다. ISO 527에 따라 시험에 필요한 모든 설정이 이미 구성되어 있습니다. testXpert는 그 밖의 여러 관련 세부 사항도 다룹니다.
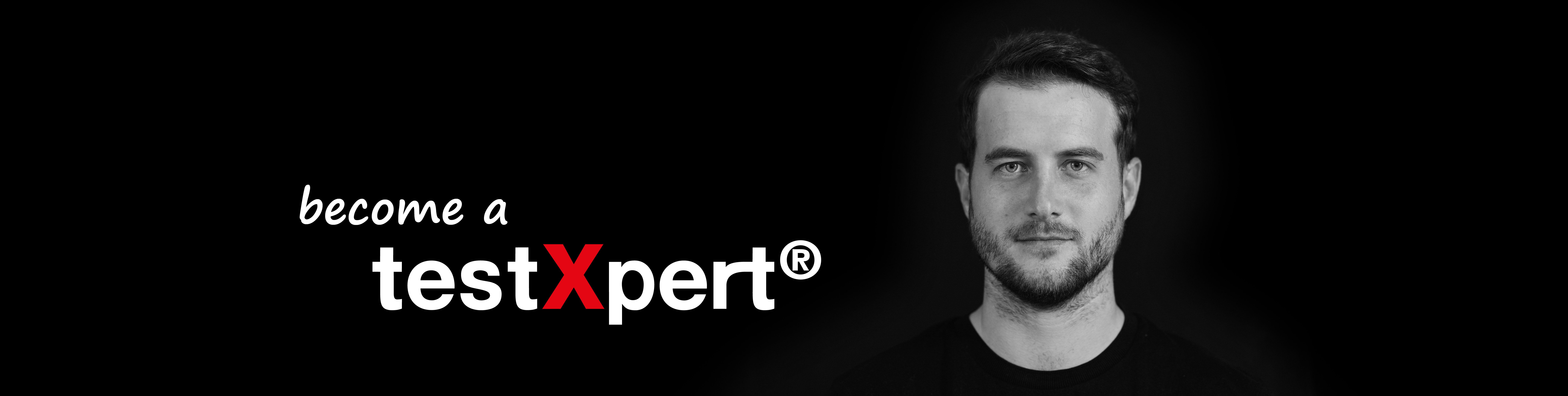
testXpert로 ISO 527 시험을 바로 시작하세요
다음과 같은 방법으로 ISO 527 시험을 효율적으로 수행하고 신입 직원을 빠르게 온보딩할 수 있습니다.
- 규격 학습의 필요성 제거: ISO 527-1/-2의 모든 물성값과 매개변수를 이미 저장한 경우 ISO 527-1/-2의 규격 시험 프로그램을 통해 규격 준수가 보장됩니다.
- 사용자 관리 기능을 통해 사용자가 시험을 진행하는 데 필요한 정보만 표시할 수 있어 ISO 527에 따른 시험을 쉽게 학습하여 안정적으로 수행할 수 있습니다. 어느 것 하나도 놓치지 않습니다.
- 주변 기기 연결을 통해 시험 효율성의 최대화를 달성합니다. 마이크로미터의 시편 치수가 시험 소프트웨어로 직접 전송되어 시간을 절약하고 입력 오류도 방지됩니다.
시편 유형 / 시편 형태
몰딩 재료 물성시험의 최우선 목표는 높은 수준의 재현성을 달성하는 것입니다. 이를 위해서는 시편 유형 개수를 제한해야 합니다. 시편의 형태와 치수는 ISO 527-2에 정의되어 있습니다. 1A형(사출 성형)과 1B형(압축 또는 기계 가공) 시편이 선호됨:
ISO 527-2에 따른 1A형 시편
- 시편은 대부분 사출 성형으로 제작됩니다. ISO 527-2에 정의된 1A형 시편이 사용됩니다. ISO 3167 에서는 A형 시편으로 정의되어 있으며 4mm의 지정된 두께로 제한됩니다. 또한, 이 시편은 A1 시편으로 ISO 20753에 포함되어 있습니다.
- 사출 성형된 시편은 피드 포인트(feed point)와의 거리가 늘어날수록 배향은 감소해 시편 길이를 따라 나타나는 기계적 성질 곡선이 일정하지 않으므로 게이트와 떨어진 곳에서 시편 파단이 자주 발생합니다.
- 시편의 권장 표점 거리는 75mm 또는 50mm입니다.
IB형 시편
- 아니면 1B형 시편을 사용할 수도 있습니다. ISO 3167에서는 B형, ISO 20753에서는 A2형으로 지정하고 있습니다.
- 이 시편들은 일반적으로 가압 또는 사출 성형된 판으로 가공됩니다. 폴리머의 배향은 대부분 사출 성형된 시편의 배향과는 매우 다릅니다. 다른 시편 형태를 이용하여 획득한 결과의 비교 가능성은 보장되지 않습니다.
- 1B형 시편은 반경이 클수록 평행 영역이 짧기 때문에 표점 거리가 50mm로 지정됩니다.
시편 치수
- 시편 치수를 측정하면 상대적으로 많은 수의 응력값 오류가 발생할 수 있습니다. 시편에 인장 하중이 가해지면 응력 결과에 측정 오차가 선형적으로 반영됩니다. 시편에 굴곡 하중이 가해지면 시편 두께측정 오류에 2차 효과가 생깁니다.
- 측정 장비의 판독 정확도 외에도, 접촉 요소의 크기 및 형태와 측정 중에 가해지는 표면 압축 역시 중요한 역할을 합니다.
- 또한 시편의 단면도는 이상적인 직사각형 모양과 다를 때가 많습니다. 이는 사출 성형된 시편의 기계적 가공이나 싱크 마크 및 작은 구배 각도로 인한 각도 오류 때문일 수 있습니다.
- 여러 시험 기준은 ISO 16012 및/또는 ASTM D5947을 참조하여 치수 측정의 요구사항과 방법을 정의합니다. 개별 시험 기준에 추가 사양이 포함되는 경우도 있습니다.
- 예를 들어, 캘리퍼는 일반적으로 10mm가 넘는 경질 플라스틱의 전체 길이를 측정하는 데 사용됩니다. 측정 중 표면 압축은 확인할 수 없기 때문에, 캘리퍼의 분해능이 높아도 측정 정확도는 다소 낮은 편입니다.
- 시편의 두께와 폭은 보통 래칫이 있는 마이크로미터 스크류로 측정합니다. 접촉면은 직경 6.35mm의 평평한 원형입니다. 래칫은 측정력을 5~15N으로 제한합니다.
- 자동화 시스템에서는 두께와 폭이 단면적 측정장치로 측정됩니다. 이 장치는 측정 중에 시편을 고정하고 4개의 디지털 측정 변환기, 정해진 측정력, 그리고 센서 피트로 치수를 측정합니다.
- 연질 플라스틱 및 필름의 경우 측정력을 엄격하게 준수하는 것이 매우 중요합니다. 이를 위해서는 재화중량 지지대가 있는 디지털 두께 측정 기구를 사용해야 합니다.
조절 및 환경 조건
- 정의된 컨디셔닝 및 주변 조건의 온도 및 습도 관련 사항을 준수하는 것은 시험 결과값의 비교성을 위해 매우 중요한 사항입니다.
- 컨디셔닝 지속 시간 사양은 일반적으로 시험 대상 플라스틱의 재료 표준에서 확인할 수 있습니다.또한 몰딩 재료 물성시험에 사용되는 시편은 시험 전 최소 16시간 동안 표준 대기(표준화된 기온 및 습도 조건)에 보관해야 합니다.
- 시험용 표준 대기는 ISO 291 또는 ASTM D618에 명시된 바와 같이 정의된 표준 대기(
온대성 대기: 23 ± 2 °C, 50 ± 10% r.F.
아열대성 대기: 27 ± 2 °C, 65 ± 10% r.F)를 참조하시기 바랍니다. - 이 공차는 2등급에 부합합니다. 이 공차는 1등급에 맞추기 위해 반으로 줄인 것입니다.
- 상온은 일반적으로 18°C ~ 28°C 사이의 다소 넓은 온도 범위를 지칭합니다.
- 다양한 요구사항을 지정할 수 있는 고온이나 저온에서의 시험도 가능합니다.
힘 측정(ISO 7500-1, ASTM E4)
대부분의 시험 기준은 측정된 값에 1%의 측정 정확도를 요구합니다. 이 요구사항은 ISO 환경에서 1등급으로 분류됩니다. 오늘날 거의 대부분의 최신 시험기는 1등급 정확도나 심지어 공차가 절반 수준인 0.5등급까지 달성합니다. 따라서 시험기가 정해진 등급의 정확도를 달성하는 측정 범위가 결정적입니다. ZwickRoell의 다양한 시험기들은 측정 범위의 1/1000 정도에서 1등급을 달성합니다. 이는 동일한 시험 장비를 이용하여 설비를 재구성하지 않고도 여러 재료의 계수값과 인장 응력을 측정할 수 있다는 의미입니다.