ZwickRoell Opens Battery Testing Laboratory
E-mobility is revolutionizing transportation and is becoming an increasingly important global challenge in the face of climate change. In this context, battery testing plays a critical role in the performance, safety and acceptance of electric vehicles. The new ZwickRoell battery testing laboratory in Ulm-Einsingen, Germany, which was inaugurated on February 28, 2024 is ready for the task. Battery developers and manufacturers are provided an overview of testing machines and can have mechanical tests performed to optimize the range, charging efficiency and temperature resistance of battery components.
“With the inauguration of our new battery testing lab, we’re taking another important step towards our customer-centric focus and innovation leadership, and underlining our commitment to excellence in battery testing and development.
We guarantee not only flexible and dynamic customer support, but also confidentiality and security when dealing with sensitive data and health-critical processes.”
Christine Dübler, Chief Sales & Service Officer at ZwickRoell
Testing of cell components and complete battery cells
The new battery testing laboratory is equipped with the state-of-the-art testing technology that covers different mechanical battery tests for cell characterization both in the field of research and development and in battery production.
The new ZwickRoell battery testing lab offers a variety of testing options:
- Testing at the cell component level, including foil/film tensile tests and adhesion tests on electrodes
- Tests on complete battery cells, also under controlled temperature conditions (e.g., battery swelling test)
- Tensile strength tests on separators, copper and aluminum foil and housing components
- Testing of weld-seam and seal strength
- Tests on shear strength of weld seams and terminals
- Puncture test on separator foil
- Adhesion test of electrode coatings and insulation material
- Fatigue tests on welded joints
- Compression strength tests of batteries and battery components
- Electrical conductivity, compressibility and mechanical characteristics are measured to simulate realistic conditions
The tests serve to ensure the quality and performance of batteries in different application areas.
Upon request, ZwickRoell develops customized testing concepts, offers advice on battery testing-related questions and performs tests on the customer’s behalf with complete confidentiality. Moving forward, the lab will have two experienced application engineers specifically dedicated to this field to provide consulting support and run the battery tests.
Are you interested in running pretests in our battery testing laboratory? Do you have questions about battery testing and would like advice from our experts?
Our application engineers are here to help.
Grand opening of the battery testing laboratory at the E-Mobility Testing Symposium
The grand opening of the state-of-the-art battery testing laboratory was attended by approximately 90 guests during the E-Mobility Testing Symposium at ZwickRoell’s headquarters. Among those present were representatives from research institutes and companies, including
Karlsruhe Institute of Technology (KIT), Cellforce Group GmbH, MBTS GmbH and Northvolt AB.
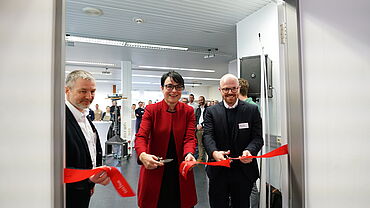
“The laboratory represents an important milestone for the entire industry and is a source of inspiration to all of us who are dedicated to shaping the future of electromobility. It is proof of our determination to drive forward innovative testing solutions and to push the boundaries of what is possible. With this laboratory, we at ZwickRoell are taking our R&D activities to a new level and contributing to the transformation of the mobility landscape.”
Aleksander Koprivc, Business Development Manager Automotive-Electrification at ZwickRoell