Wytrzymałość eksploatacyjna
Wytrzymałość eksploatacyjna to termin wywodzący się z inżynierii materiałowej i opisujący obliczoną żywotność komponentu. Wytrzymałość eksploatacyjna opisuje zdolność materiałów i komponentów do wytrzymywania obciążeń statycznych, quasi-statycznych i dynamicznych (powtarzających się lub uderzeniowych) bez uszkodzeń w obliczonym okresie użytkowania i przy uwzględnieniu odpowiednich warunków środowiskowych.
Metody wytrzymałości eksploatacyjnej mogą mieć charakter zarówno obliczeniowy, jak i wyników doświadczalnych. Wytrzymałość eksploatacyjna jest zatem nauką przekrojową, obejmującą interakcję obciążenia (mechanicznego i środowiskowego), materiału, produkcji i konstrukcji.
Naprężenia dynamiczne są prawie zawsze przyczyną awarii podzespołów. Awaria często występuje przy obciążeniach znacznie niższych od obciążenia niszczącego ustalonego w statycznej próbie rozciągania. Wytrzymałość na wibracje, jako część wytrzymałości eksploatacyjnej, opisuje zachowanie materiałów pod wpływem odkształceń i uszkodzeń pod cyklicznym obciążeniem.
Liczbę cykli wibracji, jaką element może wytrzymać pod obciążeniem roboczym, zanim nastąpi awaria, można przewidzieć ze statystyczną dokładnością za pomocą krzywej Wöhlera .
Wytrzymałość eksploatacyjna komponentu Określenie eksperymentalne Badania uzupełniające Standaryzowane sekwencje obciążeń Maszyny wytrzymałościowe
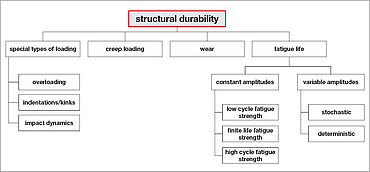
Wytrzymałość eksploatacyjna komponentu
Prace rozwojowe często nie polegają na projektowaniu komponentu tak, aby był trwały, ale funkcjonalny.
Aby określić wytrzymałość eksploatacyjną elementu, należy wziąć pod uwagę wszystkie rodzaje naprężeń , od statycznego naprężenia pełzającego , przez obciążenia uderzeniowe , po naprężenia oscylacyjne o stałej lub zmiennej amplitudzie. Uwzględniane są również warunki otoczenia i środowiska , takie jak temperatura, opady, ciśnienie, a także zmiany w materiale spowodowane korozją lub starzeniem . Wyzwaniem jest zastosowanie jak najprostszych testów w celu określenia wartości charakterystycznych, które projektant może wykorzystać, aby zaprojektować komponent tak, aby był niezawodny w działaniu.
Problem w tym, że proces uszkodzenia jest bardzo złożony i nie da się go opisać jednym parametrem. Na początku zawsze powstają mikropęknięcia, począwszy od wad wewnętrznych lub karbów, powstałych na skutek budowy lub produkcji, gdzie następuje cykliczne odkształcenie plastyczne. Podjęto próbę opisu tego procesu za pomocą badania LCF . Następnie następuje wzrost pęknięć prowadzący do zniszczenia, w przypadku którego stosuje się metody mechaniki pękania.
Z drugiej strony badanie zmęczeniowe (także badanie Wöhlera) nie rozróżnia między inicjacją rysy i wzrostem rysy. Za pomocą krzywej Wöhlera można stosunkowo łatwo przewidzieć żywotność przy zmiennych amplitudach obciążenia, stosując metody akumulacji uszkodzeń (np. Plamgren/Miner).
Na koniec pozostaje jednak jeszcze test komponentów w celu weryfikacji, choć przy znacznie mniejszym wysiłku dzięki nowoczesnym metodom charakteryzacji materiałów.
Obecnie wytrzymałość eksploatacyjna jest testowana w prawie wszystkich obszarach technologii. Wykorzystanie wytrzymałości eksploatacyjnej oferuje pewne korzyści, szczególnie w przypadku lekkich konstrukcji. Komponenty wymagają mniej materiału i dlatego mają mniejszą masę, jeśli są zaprojektowane tak, aby były funkcjonalne, a nie trwałe. Na przykład w przemyśle motoryzacyjnym lżejszy pojazd pozwala zaoszczędzić paliwo, ale lżejsza konstrukcja pozwala również na większą ładowność. Konstrukcja stabilna eksploatacyjnie również częściowo spełnia swoją funkcję: samoloty projektowane na zawsze nie mogłyby latać, bo byłyby po prostu za ciężkie.
Rozwój komponentu
Prawie każdy element maszyny, systemu lub pojazdu jest narażony na naprężenia mechaniczne, które zmieniają się w czasie podczas pracy. Zadaniem rozwoju jest wytworzenie produktu, który będzie spełniał swoją funkcję przez cały okres użytkowania. Często równoważy to krótki czas rozwoju, wymagania dotyczące lekkiej konstrukcji i ekonomiczna produkcja. Zastosowanie matematycznego szacowania trwałości w badaniach zmęczeniowych pomaga w bezpiecznym i ekonomicznym projektowaniu komponentów. Mechanika pękania zmęczeniowego umożliwia również opis wzrostu pęknięć. Kluczowe dane z badań nieniszczących można również uwzględnić w rozwoju produktu.
Celem niezawodnego komponentu jest
- osiągnięcie wymaganej żywotności
- niezawodność elementów konstrukcji lub całego systemu
- zabezpieczenie przed awarią przed osiągnięciem znamionowego okresu użytkowania (prawdopodobieństwo awarii)
Eksperymentalne wyznaczanie wytrzymałości eksploatacyjnej
Żywotność komponentu zależy nie tylko od poziomu obciążenia, ale także od kolejności obciążeń. Gdy komponent jest zaprojektowany tak, aby był stabilny eksploatacyjnie, krzywe czasu obciążenia podobne do działania (sekwencje obciążeń o zmiennych amplitudach) dostarczają bardziej wiarygodnych informacji na temat trwałości użytkowej niż badania z obciążeniami monotonnymi.
Badania uzupełniające
Z punktu widzenia wytrzymałości eksploatacyjnej przeprowadza się tzw. badania uzupełniające, podczas których zarejestrowany sygnał czasu obciążenia ma zostać jak najdokładniej odtworzony na stanowisku badawczym. Zachowanie stanowiska badawczego i komponentu oznacza, że rzeczywisty sygnał nie odpowiada pożądanemu sygnałowi docelowemu, pomimo optymalnego ustawienia regulatora. Aby poprawić dalsze zachowanie (zgodność pomiędzy sygnałami zadanymi i rzeczywistymi), sygnał docelowy jest zmieniany w procesie iteracyjnym, aż sygnał rzeczywisty będzie odpowiadał pierwotnemu sygnałowi docelowemu.
Badania ze znormalizowanymi sekwencjami obciążeń
Znormalizowane sekwencje obciążeń wyprowadzono dla typowych zastosowań projektowych z dużej liczby reprezentatywnych pomiarów naprężeń eksploatacyjnych i służą one na arenie międzynarodowej jako podstawa do obliczania komponentów obciążonych dynamicznie.
Odpowiednie produkty do określania wytrzymałości eksploatacyjnej
Różne materiały i komponenty wymagają różnych technologii badawczych . W ostatnich latach firma ZwickRoell ogromnie zainwestowała w rozwój maszyn do badań dynamicznych i technologii napędowych i oferuje odpowiednią koncepcję napędu do każdego zastosowania badawczego:
- Elektromechaniczne cylindry serwo oferują koncepcję modułową dla niskich częstotliwości do 1 Hz i 50 kN
- Linear Testing Maschine LTM to seria elektrodynamicznych maszyn wytrzymałościowych, których napęd oparty jest na technologii silników liniowych. Napęd został opracowany specjalnie do celów badania technologii i jest opatentowany przez firmę ZwickRoell
- Rezonansowe maszyny badawcze serii Vibrophore, które oferują bardzo wysokie częstotliwości badawcze przy bardzo niskich kosztach eksploatacji. Możliwe są częstotliwości badawcze do 285 Hz.
- Serwohydrauliczne maszyny wytrzymałościowe ze znormalizowaną koncepcją ramy obciążeniowej oferują największą elastyczność w każdym zastosowaniu
Ze względu na tę różnorodność technologii napędowych ZwickRoell jest jedynym producentem maszyn badawczych, który może udzielić neutralnych porad na temat koncepcji napędu. We wszystkich maszynach testujących stosowane jest to samo oprogramowanie badawcze i technologia kontrolera. Oznacza to, że codzienna praca laboratoryjna nie wymaga dużego szkolenia .
Wszystkie wymienione powyżej maszyny wytrzymałościowe mogą być stosowane zarówno jako statyczne jak i jako dynamiczne maszyny wytrzymałościowe . Jest to możliwe dzięki wspólnemu zastosowaniu elektroniki testControl II i sprawdzonego oprogramowania badawczego testXpert.
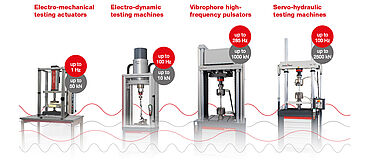