Hardness Testers
ZwickRoell offers a comprehensive portfolio of hardness testers for tests on metals, ceramics, plastics, rubber and special materials. These instruments meet the requirements of all relevant hardness test methods and internationally accepted standards. With our ISO/IEC 17025 UKAS and DAkkS accredited calibration laboratories, ZwickRoell guarantees precise and certified hardness testing.
With the level of expertise provided by EMCO-TEST, we combine more than 70 years of expertise in hardness testing under one roof. This is our basis for progressive solutions and innovative approaches that define new standards—made in Europe.
The differences between hardness testers lie primarily in the test methods, such as Rockwell, Vickers, Brinell and Knoop, which have a decisive influence on the design of the hardness testing machine. Get an overview of the different hardness tester model series and their areas of application. Our portfolio of hardness testers includes solutions ranging from standard manual applications to fully automatic hardness testing systems:
Vickers Universal Rockwell Brinell Knoop Portable hardness tester SHORE/IRHD
Accessories & test plates Automation, customization, special systems Hardness standards overview Customer projects Request a consultation
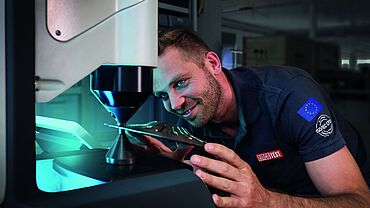
Hardness testing worldwide
We have representation in more than 50 countries and offer our customers fast and reliable hardness testing solutions. With over 100 experts in this field
, we support our customers in testing the durability and reliability of their products.
Intelligent testing solutions
We offer the right solution for every one of your test tasks: starting with standard test methods for customized test sequences, to changing test tasks within a testing system, all the way to fully automated, complex test processes.
Vickers hardness tester
Vickers hardness testing machines are ideal for thin, hard materials, surface layers and offer high precision for micro hardness measurements. A diamond pyramid is used to create an impression in the material to be tested and then evaluated visually. For series tests, the hardness tester requires an additional precise system to position the test specimen. Fully automated systems with a motor-driven axis for precise test point placement are particularly efficient.
Our DuraScan series offers you all the functions and advantages you need for Vickers hardness testing.
DuraScan hardness tester
The DuraScan series is your efficient laboratory companion in the low load and micro hardness range. The standard load range of 10 gf up to 62.5 kgf is applied with a closed loop and can optionally be extended to 0.25 gf up to 62.5 kgf. In addition to Vickers hardness testing—the most commonly used test method—the DuraScan low load and micro hardness testing machines can also be used for Knoop and Brinell test tasks. Our DuraScan series has an automatic 6-position turret that allows you to quickly change your indenters and lenses.
- Applications: DuraScan hardness testers are ideal for series tests on embedded specimens, such as welding samples or hardened specimens. With the low load levels, you can also test very thin materials and coatings. Additional modules also make it possible to test special components such as pipe segments or tooth flanks.
- Standards: Vickers ISO 6507, ASTM E92, ASTM E384, Brinell ISO 6506, ASTM E10, Knoop ISO 4545, ASTM E92, ASTM E384
More on Vickers hardness testers More on the DuraScan series
Universal hardness testers
Universal hardness testers are designed for hardness testing according to Brinell, Vickers, Rockwell and Knoop, as well as for plastics testing and carbon testing. To cover all of these test methods, the universal hardness testing machine supports a wide load range.
Our Vision series covers a uniquely wide standard load range of 0.3-250 kgf or 3-3000 kgf (optionally from 0.01 kg), which supports a large number of test methods.
Vision Universal Hardness Tester
The Vision universal hardness tester for standard load ranges of 0.3-250 kgf or 3-3,000 kgf (optionally from 0.01 kg) can be used for Vickers, Knoop, Brinell, and Rockwell tests, as well as for carbon and plastics testing. All methods are covered by the ISO 6506, ISO 6507, ISO 45452, ASTM E384, ASTM E92, ASTM E10, ISO 6508, ASTM E18, DIN 51917 and ISO 2039 standards.
The Vision hardness testers are available in a handwheel version with motorized Z-axis or as a fully automatic hardness tester for use in the production environment, in the laboratory for quality assurance, as well as in harsh production environments.
Rockwell hardness testers
Rockwell hardness testers are ideal for metallic materials and are characterized by their quick and easy handling. Rockwell hardness testers use a depth measurement procedure and require suitable and calibrated measuring equipment.
With the DuraJet Rockwell hardness tester and the simple N3 Rockwell tester, we cover the full Rockwell range and additionally support plastics and carbon testing as well as HVT and HBT.
Brinell hardness testers
Brinell hardness testers measure hardness by indenting the material with a carbide metal ball. The indentation is then visually evaluated. The Brinell method is ideal for relatively soft and inhomogeneous materials. The surface requirements are relatively low, especially for high test loads of up to 3,000 kg.
Our VisionLine hardness testers cover a wide range of Brinell methods.
Knoop hardness testers
The Knoop hardness test is an alternative to Vickers hardness testing for low test forces. It is primarily used to prevent cracking in brittle materials such as ceramics, but also to facilitate the testing of thin layers.
Knoop hardness testers therefore use a rhombic indenter made of diamond for micro hardness measurements. The evaluation is carried out visually. Our DuraScan series hardness testers are the perfect solution for Knoop hardness tests. They meet all applicable standards such as ASTM E384 and ISO 4545.
More on Vickers hardness testers More on the DuraScan series
Portable hardness tester for metals
Portable Rockwell hardness testers in a load range of 15 to 187.5 kgf have proven themselves in many branches of industry (e.g., energy, shipbuilding, mining, large-scale plant construction, petroleum and petrochemicals) for decades. Their high level of flexibility makes them ideal for measurements directly on the object to be tested, or for locations that are difficult to access. Applications range from the simple measurement of sheet metal to hardness tests on tooth flanks and drill holes.
At the core of every portable Rockwell hardness tester is the reliable spring sleeve system for load application. The hardness value is indicated on an analog dial gauge.
More on portable Rockwell hardness testers:
- N4 - testing clamp for sheet metal, plates, etc.
- N6 - hardness tester for drill holes
- N7 - tooth flanks - hardness tester for tests on tooth flanks
Portable hardness testers for plastics and rubber
Plastics hardness testing according to Shore (durometer) and IRHD test the hardness of rubber, elastomers, plastics and similar materials. The penetration depth is measured by an indenter that penetrates the material/specimen. This is essential for quality control purposes in the rubber and plastics industry.
ZwickRoell offers portable hardness testers for plastics and elastomers in different versions (analog/digital and with/without support bracket/stand). They meet the applicable standards, such as ASTM D2240 & ISO 48-4, ISO 868, NFT 51 123, NF 46 003 and ASTM D1415 & ISO 48-2.
Automation, customizing, special systems
At ZwickRoell, we understand the uniqueness of every requirement in materials testing. That is why we design our hardness testing machines and comprehensive accessories portfolio to be seamlessly tailored to the specific needs of our customers. Regardless of whether they are standard hardness testers or whether special adaptations are required, we offer individually modifiable accessories and customized solutions to precisely and efficiently handle any testing task.
In close collaboration with our customers, we develop solutions that are not only functional and efficient, but also reliable—always in compliance with applicable legal requirements. With innovative features such as signaling systems to monitor the operating status and external operating options for remote control of your machine, we guarantee use that is both simple and safe.
- Customizing
Our hardness testing machines and accessories such as test anvils, specimen grips and probes can be customized to enable efficient component testing in accordance with international standards. - Special systems
For very specific requirements, we design systems that are completely tailored to your particular needs. Automated test processes and the evaluation of test points, supplemented by milling devices for specimen surface preparation, are a matter of course for us and part of our solution expertise. - Automation
In close collaboration with our customers we have automated the full hardness testing process. Our automated testing systems, which are essential for modern testing laboratory environments, take over specimen handling and reliably run tests according to standards requirements.
Accessories & test plates
A hardness tester is an important tool for materials testing and analysis. By adding the right accessories, the instrument becomes even more effective and ready to meet individual requirements. Some of the accessories we offer include:
- Test anvils
- Indenters
- Lenses
- Nose cone inserts
- Hand-held scanner
- Foot switch, and much more
Hardness reference blocks
Hardness reference blocks are essential for calibration and daily checks of hardness testers to ensure their operational reliability. They must have a minimum hardness deviation and be precisely calibrated. ZwickRoell offers these blocks, which are calibrated in a UKAS accredited laboratory in accordance with strict standards to meet the requirements of different industries worldwide.
Important standards for hardness testing
Hardness testing is an important part of quality assurance, and standards such as ISO 6506, ISO 6507, ISO 6508, ASTM E10, ASTM E384 and ASTM E18 provide the decisive guidelines. These standards precisely define the respective methods to ensure that the results are reliable and internationally reproducible. In this section, we will discuss the most common standards and their importance in carrying out accurate and standardized hardness tests in various industries.
All of our hardness testers guarantee compliance with all applicable ISO and ASTM standards ISO standards and ASTM standards .
- ISO 6506 - Brinell method: The Brinell method, which is defined in ISO 6506, is ideal for larger, coarse-grained materials. A carbide metal ball is pressed into the material and the indentation is measured to determine the hardness. This method is widely used in the metals industry.
- ASTM E10 - Brinell method: ASTM E10 is a standard that describes the Brinell method in parallel to ISO 6506 and is common specifically in the US. It is mainly used for materials such as steel and iron alloys.
- ISO 6507 - Vickers method: ISO 6507 describes the Vickers method, which is characterized by its applicability to a wide range of material hardnesses. A pyramid-shaped diamond indenter is used to create a small indentation that is analyzed for hardness determination.
- ASTM E384 - Vickers and Knoop micro hardness test method: ASTM E384 covers micro hardness measurements, ideal for very small specimens or thin surface layers. It allows for precise measurements on a microscopic level with specialized indenters.
- ISO 6508 - Rockwell method: The Rockwell method specified in ISO 6508 is known for being quick and uncomplicated. It measures the indentation depth of an indenter under load and is perfectly suited for medium hard to hard materials. Diamond cones and carbide metal balls are used as indenters, depending on the corresponding scale.
- ASTM E18 - Rockwell method: ASTM E18 presents guidelines particularly aimed at the Rockwell method for the US. It is one of the most commonly used methods in materials testing, especially for harder materials.
Frequently asked questions about hardness testers
A hardness tester is a device or instrument used to test the material hardness at the respective measuring point or to determine the resistance of a material to deformation. Hardness testers are used in material production and processing throughout the supply chain to ensure that materials, mainly metals, non-ferrous metals and plastics, meet the required material properties.
During a hardness test, the hardness tester presses an indenter, usually made of diamond or hard metal, into the surface of the test specimen with a very precise force and for a specifically defined duration. The resulting indentation is evaluated either visually using a microscope, or by measuring the penetration depth of the measuring head. Choosing the appropriate hardness test method and therefore also the right hardness tester depends on various factors, such as the type of material, the expected hardness, the surface condition and the precision required for the measurement.
When choosing a hardness testing machine, you should consider the type of material to be tested, the required standards and the specific requirements of your application. The operating concept of the hardness tester contributes significantly to the operation efficiency and should therefore be taken into account. The throughput rates may influence the decision for possible automation. Standard interfaces enable connection to your own databases. It is also important that the hardness tester has the required calibration.